Electric furnaces mainly use scrap steel as the main raw material for steelmaking. When scrap steel, lime, etc. are added into the furnace when the electricity is turned on, an electric arc occurs between the graphite electrode and the scrap steel, and the charge is heated. Then a series of metallurgical chemical reactions are carried out to make the scrap steel into steel. Electric furnaces mainly include DC electric arc furnaces, AC electric arc furnaces, and induction furnaces. The use of refractory materials for the bottom of the electric furnace depends on the size of the electric furnace. Refractory materials used in the furnace bottom include magnesite bricks, magnesia carbon bricks, and magnesia dry ramming materials.
The history of AC electric arc furnace steelmaking is relatively long, so its refractory materials for furnace bottom have also undergone changes. The bottom of the furnace was rammed with asphalt tar magnesia or brine magnesia ramming mass material. Because the bottom of the brine magnesia is corroded quickly, it cannot meet the requirements of use. Although bituminous tar magnesia has better durability, it is troublesome to construct and causes environmental pollution. Therefore, more magnesite refractory bricks and low-grade magnesia-carbon bricks were subsequently used to build furnace bottoms. The brick furnace bottom is very durable, but the masonry is labor-intensive and time-consuming. Sometimes, if the masonry is not good enough, the bricks will rise and cause production to stop.
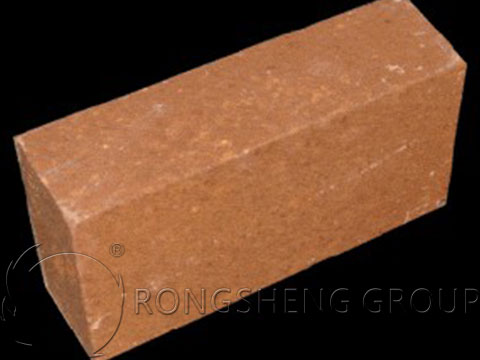
Use of furnace bottom dry ramming material. Its construction is simple and convenient, without baking, after construction, it can be directly used for steelmaking. The material is a dry vibrating ramming material of the magnesium-calcium-iron series. Using the low melting point calcium ferrite it contains, it can quickly sinter to produce strength when the temperature rises above 1200°C. Under the hydraulic pressure of molten steel, it can quickly sinter and shrink, and its shrinkage can reach 4% to 5%, and the bulk density can increase to more than 3.0 g/cm3. Has particularly good corrosion resistance and good results.
Refractory material consumption per ton of steel has been reduced from 4-8 kg of asphalt magnesia bricks to less than 2 kg. Some modern electric arc furnace bottom dry materials consume as little as 0.3 kg per ton of steel, which mainly corresponds to the steelmaking technology. During use, the material is sintered layer by layer, sintered and densified near the molten steel, and resists corrosion and erosion by molten steel. Below the sintered layer is the transition layer, and then the loose unsintered layer. This loose layer has a low density and low thermal conductivity, which plays an important role in the insulation of the electric arc furnace. After years of promotion and development, most of our country’s electric furnace bottoms use this ramming material.
The construction and use of the furnace bottom dry materials are the key factors that affect the use effect. The furnace bottom material should be called dry vibrating refractory castable, which is more appropriate. Because the vibration densification density of the material is 0.2g/cm3 higher than that of ramming, it will significantly improve the corrosion resistance. The refractory manufacturer believes that the dry material should be vibrated for construction, especially for the DC electric arc furnace bottom that is not easy to repair. When repairing, the slag and scrap at the bottom of the furnace must be cleaned up. Otherwise, the steel slag under the repair material may melt when used to a certain extent, and the bottom material will float under the impact of the steel block. During tapping, the floating bottom block may block the tapping port and affect tapping. During use, the bottom of the furnace should be observed at any time, and if it rises, it should be repaired in time. Generally, use the same kind of material to fill the pit. To prevent further expansion of the floating and prevent the occurrence of the phenomenon of steel breakout.
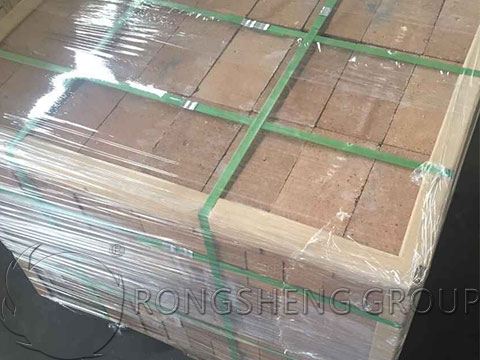
The bottom of the electric furnace and the slope of the embankment together form a molten pool. Its refractory materials directly bear high-temperature thermal load and erosion from molten slag, molten steel erosion, the mechanical impact of scrap steel, and oxidation and reduction operations at high temperatures in the furnace. The slag penetrates to the bottom of the furnace, resulting in thinning of the bottom of the furnace.
The structure of the ultra-high-power electric furnace bottom is generally divided into three layers.
- ①The heat insulation layer is the lowest layer of the furnace bottom, its function is to reduce the heat loss of the electric furnace, and to ensure that the temperature difference between the upper and lower sides of the molten pool is reduced. Generally, a layer of the asbestos board is first laid on the furnace shell, and then diatomaceous earth powder, on which insulation bricks are laid flat.
- ②The permanent layer is on the heat insulation layer, its function is to ensure the solidity of the molten pool, and play the role of supporting the bottom. It is generally built with bricks, with about 3 layers of staggered joints. Use 95%-96% MgO-fired magnesia bricks, asphalt bonded magnesia bricks, magnesia dolomite bricks, etc. Fill the brick joints with magnesia or steel powder of the same material, squeeze, and compact.
- ③The working layer is above the permanent layer, and it is in direct contact with molten steel. High thermal load, severe chemical erosion, strong mechanical erosion, and extremely easy to be corroded, high-quality refractory materials should be used. The working layer of the electric furnace bottom in our country is built with ramming furnace bottom or burnt magnesite bricks combined with asphalt, magnesia sintered or fused, dolomite calcined.
At present, ultra-high power electric furnaces generally use a mixture of 2CaO·Fe2O-rich magnesia and 2CaO·Fe2O-rich magnesia dolomite (without any binder). Ramming (actually the lower bunk) into a whole structure furnace bottom, its durability is high.
There are usually two types of ordinary power electric furnace bottoms.
- ①Knotted furnace bottom (or vibration compression furnace bottom). The working layer uses magnesia, and its bonding agent is tar and asphalt. When making the carbonless furnace lining, brine or water glass is used as the bonding agent.
- ② Brick furnace bottom. Generally, asphalt is used to combine magnesite bricks, and carbon-free furnace lining is used to combine magnesite bricks with brine.
Commonly used refractory materials for electric furnaces include diatomaceous earth bricks, lightweight insulation bricks, and magnesite bricks. For the price of high-quality refractory lining materials, please contact us.