Silicon carbide refractory castables are the development of SiC refractory products (bricks, plates, rods, tubes, saggers, etc.). Usually, SiC refractory castables are designed with low cement and ultra-low cement formulations. SiC is used as the main raw material, and aluminum cement (CA-70C or CA-80C, etc.) and nf-SiO2 and Al2O3 micro powder are used as binders. However, the production of SiC-based monolithic refractory materials, especially SiC-based refractory castables, encounters the following problems.
- (1) SiC is hydrophobic. As a result, the fluidity of the SiC refractory castable is poor, the construction performance is not good, and the density of the cast body is low.
- (2) SiC is difficult to sinter. Therefore, it is not easy to obtain a high-strength sintered body.
In order to improve the fluidity of silicon carbide refractory castables, it is necessary to select SiC raw materials that have little effect on fluidity as the SiC source for the production of silicon carbide refractory castables. This can be achieved by changing the shape of SiC particles and adjusting the type and amount of dispersant (water reducer) (that is, improving the fluidity and construction performance of SiC refractory castables).
For the production of SiC refractory castables, spherical SiC particles have better performance than needle-shaped SiC particles. By using uf-SiC to replace a part of the angular SiC raw material or flakes, more effective dispersants (water reducers), such as SM and sodium polyacrylate, etc. are added. It can also improve the fluidity and construction performance of SiC refractory castables.
The purpose of adding Si powder to SiC refractory castable is to improve the oxidation resistance of the material. The particle-optimized SiC granular material was once used as a binder with 75% AI2O3 pure alumina cement as a binder, and Uf-SiO2 (95% SiO2) as an auxiliary binder to form a hydration coagulation binding system for the refractory casting material. The effect of adding different amounts of Si powder on the oxidation resistance of SiC refractory casting materials was studied. The results show that when the amount of Si powder added is 2%, the SiC refractory castable has the best oxidation resistance.
The Uf-SiO2 is used in the silicon carbide refractory castable combination system mainly to improve the physical properties of the material. When the amount of Uf-SiO2 added reaches a certain value, the refractory castable will have higher strength, especially after the medium temperature treatment, the strength will increase by nearly 1 time, and the mixing water consumption of the material will be reduced by more than 0.9%.
When phosphate is used as the water reducer, the SiC refractory castable has better physical indicators.
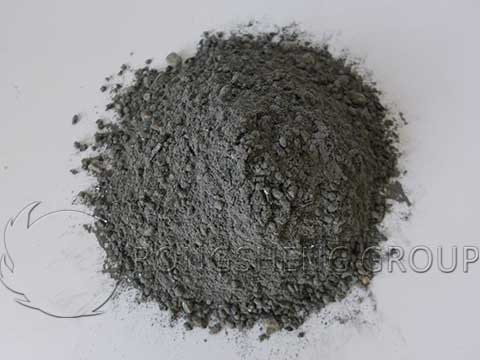
Application characteristics of silicon carbide refractory castable
Silicon carbide refractory castable has stable properties, excellent corrosion resistance, and wear resistance. It is not corroded by boiling hydrochloric acid, sulfuric acid, or hydrofluoric acid. It will not be oxidized when used in a reducing atmosphere at a temperature of 1600°C, but it will be oxidized in an oxidizing atmosphere.
The use of silicon carbide castables at a temperature of 800-1140°C is not as good as at 1300-1500°C. Because in the range of 800-1140°C, the structure of the oxide film formed by oxidation is loose, and it cannot play the role of silicon carbide. However, above 1140°C, especially between 1300-1500°C, the oxide film formed by oxidation covers the surface of the silicon carbide substrate, hindering the contact of oxygen with silicon carbide. Therefore, in the temperature range of 1300-1500 ℃, the oxidation resistance is the best. However, when the temperature exceeds 1500°C, the oxidation protection layer will be destroyed. At this time, the silicon carbide castable will be strongly oxidized, and the matrix will be decomposed and destroyed.
Silicon carbide castables are hard materials with high hardness. Good creep resistance, thermal shock resistance, and wear resistance, but high thermal conductivity. However, silicon carbide castables also have different qualities, that is, different proportions of silicon carbide are added. But no matter what kind of castable it is, metal silicon powder should be added to adjust it to resist oxidation and decomposition, refractory bricks, which also need to be adjusted to prevent oxidation.
In fact, silicon carbide castables are composite castables, which are made by mixing with alumina aggregate and powder, adding a certain proportion of silicon carbide and binder. So it’s all compound.
Generally, it is used in furnace linings with serious erosion. If the temperature is lower than the furnace lining below 1300°C, silicon carbide refractory castables should not be used. The furnace lining under the condition of oxidizing atmosphere is not suitable for this kind of castable. It is better to use the reducing atmosphere lining at 1300-1500 ℃.
Contact us for more refractory castable details.