The main component of magnesia bricks is magnesium oxide, and there are many varieties of magnesia refractory bricks. There are corresponding branches according to the production process. Rongsheng Refractory Materials Manufacturer can provide high-quality magnesia bricks, magnesia-chrome bricks, direct-bonded magnesia-chrome bricks, etc. Regarding directly bonded magnesia-chromium bricks, what are their characteristics and application fields, and what are their application effects?
Directly bonded Magnesia Chrome Bricks
Magnesia bricks are widely used. Among them, high-temperature industrial kilns use directly bonded magnesia-chromium bricks, which are divided into four grades: ZMGe-8, ZMGe-12, ZMGe-16, and ZMGe-20 according to physical and chemical indicators. It has the characteristics of high structural strength at high temperatures, high softening temperature under load, and strong resistance to chemical erosion. Main uses: Widely used in cement rotary kiln firing belts, glass melting furnaces, steelmaking electric furnaces, converters, and non-ferrous metal smelting furnaces.
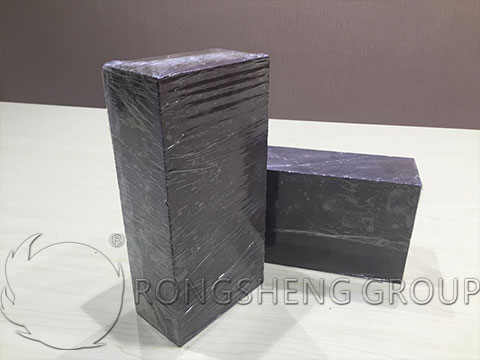
When producing direct bonded magnesia-chromium bricks, chrome ore with low SiO2 content should be used as much as possible. Because the low SiO2 content is beneficial to improving the high-temperature performance of this type of refractory bricks. By comparing the performance of various magnesia-chrome bricks, it was found that the high-purity SiO2 content is low, and the load-softening temperature of the directly bonded magnesia-chrome brick produced from chrome ore is high. Of course, magnesia-chromium bricks with low SiO2 content also need to be fired at high temperature or low temperatures. As many research works have pointed out, there is no obvious dividing line between silicate-bonded (ceramic-bonded) magnesia chromium bricks and directly bonded magnesia chromium bricks. However, there is actually no direct bonding between magnesia-chromium bricks fired below 1500°C. Only when the firing temperature exceeds 1550℃, their direct combination will increase.
Since today’s magnesia-chrome bricks are fired at temperatures above 1500°C, they only differ in the degree of direct bonding. This shows that the primary condition for producing direct bonded magnesia-chromium refractory bricks is to be fired under high or warm conditions. For example, after firing at 1800°C, magnesia-chrome bricks containing 1.5% SiO2 have an increased direct bonding amount of high refractory phases compared with other magnesia-chrome bricks. However, excessively high firing temperatures will also cause this type of magnesia-chromium bricks to deform and stack, thereby increasing the amount of waste refractory bricks.
In order to reduce waste products caused by firing deformation, the measure taken in process technology is to reduce the SiO2 content in the ingredients, especially the SiO2 content in chromium ore. The direct bonding amount in magnesia chrome bricks increases significantly with the decrease in SiO2 content. This is because when the SiO2 content decreases, the silicate layer in the material is replaced by direct bonding between high-refractory phase crystals.
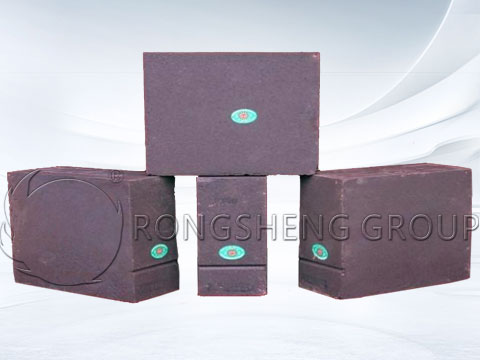
The Difference between directly Bonded Magnesia Chrome Bricks and Ordinary Magnesia Chrome Bricks
- 1. Ordinary magnesia chrome bricks contain MgO 55~80%, Cr2O3 ≥8%, generally 8~20%. The main minerals are periclase and chromium spinel, and the silicate phases are forsterite and forsterite. If the Cr2O3 content is as high as 18~30% and MgO 25~55%, it is called chromium magnesia brick. Note: Cr2O3 ≥ 20% is equivalent to adding more than 50% chromite to the ingredients. Cr2O3 ≥ 8% is equivalent to adding more than 20%.
- 2. Directly bonded magnesia-chromium bricks can be used in large kilns with kiln temperatures above 1700°C. Ordinary magnesia chrome bricks are no longer suitable. Directly bonded magnesia-chromium brick is a magnesia-chromium refractory material developed to adapt to large-scale cement production.
The main minerals of directly bonded magnesia chromium bricks, periclase, and spinel, are mostly directly bonded. Although there is also a small amount of silicate phase matrix, the direct bonding rate is high. Therefore, the high-temperature performance of the refractory brick body is greatly improved. Directly bonded magnesia-chromium bricks are made of magnesite ore and chromite ore as raw materials, which are first fired into light-burned magnesia and then pelletized under high pressure after being graded to a certain level. It is fired into dead burnt magnesia at a high temperature of 1900°C, then mixed with a certain proportion of chromite ore and pressed into shape. It is calcined in a tunnel kiln at 1750~1850℃. Those fired at 1750~1800℃ are high-temperature direct bonded magnesia chromium bricks. Those fired at 1800~1850℃ are warm direct bonded magnesia chromium bricks.
Why is the load-softening temperature of directly bonded magnesia chromium bricks smaller than that of directly bonded magnesia bricks?
Due to the different raw material purity and ratio of magnesia brick products, the load and softness are also different. These can be customized according to customer needs.
Magnesia chrome bricks are divided into ordinary magnesia chrome bricks, direct bonded magnesia chrome bricks, semi-bonded magnesia chrome bricks, fused magnesia chromium bricks, fused semi-bonded magnesia chrome bricks, and unfired magnesia chrome bricks. The difference between magnesia-chrome bricks and directly bonded magnesia-chrome bricks lies in the following two aspects.
- 1: Purity of magnesia-containing sand (raw material).
- 2: Sintering temperature. The sintering temperature of ordinary magnesia chrome bricks is 1550℃~1600℃, and the sintering temperature of direct magnesia chrome bricks is above 1700℃. Because when the temperature is above 1700°C, the microstructure of magnesia-chromium bricks changes, and periclase is directly combined with chromium ore. So it is called direct bonded magnesia chromium brick. All aspects of the properties of directly bonded magnesia-chrome bricks are better than those of ordinary magnesia-chrome bricks.
Directly bonded magnesia-chromium bricks are mainly used in the refining part of the smelting industry, non-ferrous smelting, reaction furnaces, and the heat storage part of the glass industry, etc. Category: Refractory Bricks. Material: magnesium chrome. Specifications: 380*150*75/65 (mm). Zhengzhou Rongsheng Kiln Refractory Materials Co., Ltd. produces refractory bricks with complete products and reasonable prices. Contact us to get free samples and quotes.