Submerged arc furnace, also known as electric arc electric furnace or resistance electric furnace, is mainly used to reduce smelting ores, carbonaceous reducing agents and solvents and other raw materials. Submerged arc furnaces mainly produce ferrous alloys such as ferrosilicon, ferromanganese, and ferrochrome. Its working characteristic is to use carbon, aluminum, and magnesia refractory materials as furnace lining and eyebricks. However, magnesia or aluminum furnace eye bricks are easily damaged when subjected to long-term thermal load impact and silica slag erosion in the furnace. It may even cause the furnace wall to burn through, seriously affecting the normal operation of the submerged arc furnace. Therefore, furnace eye bricks with silicon carbide as the main raw material came into being.
Silicon Carbide Furnace Bricks
Silicon carbide furnace brick is a non-oxidizing high-temperature refractory material with the characteristics of high temperature resistance and corrosion resistance. Its main specifications are: SIC 90, SIC 97, etc. Advantages, material selection and performance of silicon carbide furnace eye bricks. According to the characteristics of the taphole, after comparing several commonly used refractory materials, it was found that:
AL2O3 (including AL2O3-SiC series) materials have poor thermal shock resistance, thermal conductivity, spalling resistance, and slag resistance. Graphite materials have poor wear resistance and resistance to molten iron corrosion. SiC materials have poor resistance to molten iron corrosion. Therefore, they should not be used alone as taphole refractory materials. Therefore, we chose to use semi-graphite materials as the main material, and added some artificial graphite and SiC powder to develop semi-graphite-silicon carbide bricks as refractory materials for the taphole of submerged arc furnaces.
The raw material is electrically calcined anthracite coal at 1750-2000℃. At this time, it has been semi-graphitized, and the degree of graphitization reaches 15% to 30%. It has a dense structure and high strength. Therefore, it is used as the main raw material. In order to improve the thermal conductivity, alkali resistance and formability, a small amount of artificial graphite is added. In addition, SiC is added because SiC is oxidized preferentially than carbon to form a SiO2 protective film, covering the surface. Preventing further oxidation of products can improve the oxidation resistance of carbon products. In order to improve the quality of the material, a small amount of industrial silica powder is added. During the roasting process, industrial silicon powder and carbon react Si(s)+C(s)→β-SiC(s) to produce β-SiC. It can give products higher strength and wear resistance. A small amount of unreacted Si on the pore wall reacts with the oxygen and nitrogen in the pores 4Si(s)+ 2N2 (g)+ O2 (g)→2Si2ON2 (s). Si2ON2 is a needle crystal. Make the pores narrow or close, block the pores, and reduce the air permeability of the product. Prevent the penetration of slag and iron and improve oxidation resistance.
The production process uses electric calcined anthracite, artificial graphite, SiC, and industrial Si powder with specific particle size distribution as aggregates. Coal pitch is used as a binder, which is mixed and rolled for 1.5 hours at 150~170°C, and then formed by high-frequency molding and vibration. It is then calcined in a reducing atmosphere with a maximum calcining temperature of 1300°C. The fired blanks are then cut and ground into various shapes. Due to the good thermal conductivity of semi-graphite-silicon carbide bricks, the temperature of the taphole masonry is reduced and the erosion rate is slowed down. The thermal expansion coefficient is similar to the thermal expansion coefficient of the furnace prebaked carbon block, thus avoiding the damage to the furnace lining caused by the different thermal expansion coefficients of AL2O3-SiO2 refractory materials and carbonaceous materials.
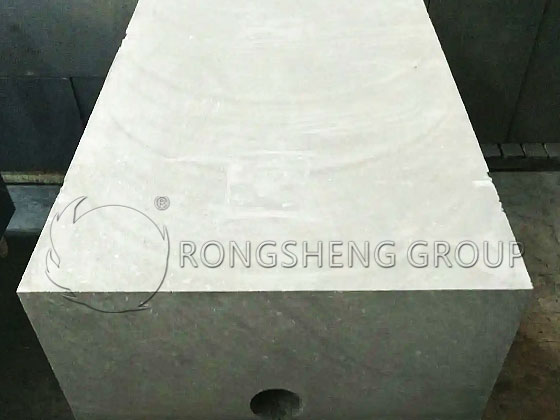
Why Use Semi-Graphite-Silicon Carbide Bricks for the Taphole of a Submerged Arc Furnace?
In the early years, submerged arc furnace taphole bricks mainly used small pieces of standard high alumina bricks or corundum bricks. Only a few large and medium-sized submerged arc furnaces used sillimanite bricks, corundum mullite bricks, and composite brown corundum bricks. Lifespan is generally shorter. The tapholes of large-scale submerged arc furnaces abroad are mostly composed of composite bricks and use high-quality refractory materials. For example, European countries use microporous carbon bricks and mullite bricks, Japan uses sillimanite bricks and AL2O3-SiO2 bricks, and North America uses hot-pressed small carbon bricks. Coupled with scientific management, operation, and maintenance, the life of the taphole will be longer. For this reason, China’s domestic refractory material manufacturers have absorbed the advantages of foreign taphole refractory materials and developed semi-graphite-silicon carbide bricks for submerged arc furnace tapholes to address the causes of damage to the tapholes of submerged arc furnaces. It has been successfully used in domestic submersible furnaces of various categories and sizes for many years.
- (1) AL2O3-SiO2 series materials such as corundum bricks and mullite bricks no longer meet the needs of strengthening the longevity of the taphole of smelting submersible furnaces in my country.
- (2) Semi-graphite-silicon carbide bricks have good thermal conductivity, thermal shock resistance, alkali resistance, spalling resistance, and resistance to erosion by molten iron and slag. Fundamentally overcome the shortcomings of Al2O3-SiO2 series materials. Due to the addition of SiC powder and the sintering process, the SiC generated by industrial Si improves the oxidation resistance.
- (3) Semi-graphite-silicon carbide bricks at the taphole of submerged arc furnaces have been used in submerged arc furnaces of different sizes in China for many years with good results.
Rongsheng Refractory Brick Manufacturer
Rongsheng Refractory Brick Manufacturer is a very powerful manufacturer and seller of refractory materials in Xinmi City, Henan Province, China. Our refractory products have been sold to more than 1,000 countries around the world. Moreover, our professional technical team can customize refractory lining material solutions based on the actual working conditions of high-temperature industrial furnaces. Our comprehensive customer service also ensures the long life and efficient use of high-temperature furnace linings. Contact us for a free solution and quote.