Unshaped refractory materials, also known as bulk refractory materials, are composed of bulk particles and fine powders. They do not need to be fired or formed before use. Unshaped refractory materials are used in many parts of blast furnace ironmaking and high-temperature furnaces in the non-ferrous metallurgical industry. Application of chrome corundum castable lining in non-ferrous metallurgical furnace melting furnace. Rongsheng Monolithic Refractory Material Production and Sales Manufacturer is a powerful refractory material production and sales enterprise. Contact Rongsheng for free samples and quotes.
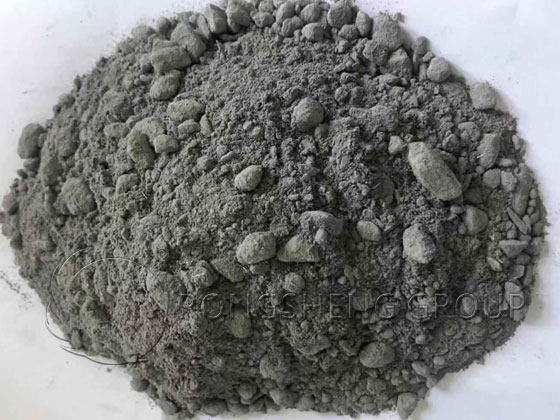
Application of Unshaped Refractory Materials in Blast Furnaces
Blast furnaces are an important equipment for ironmaking. Small blast furnaces used to be hoisted and built with prefabricated blocks of high-alumina cement and high-alumina phosphate refractory sintering materials. Now, resin-bonded aluminum-carbon unburned bricks are commonly used for masonry.
The water-cooled walls of large blast furnaces are rammed with silicon carbide castables. The bottom cushion and surrounding brick joints are made of refractory castables and silicon nitride fillers. One of the development trends of refractory materials for furnace walls is to use castables. China mainly uses corundum-silicon carbide castables. Most of Japan’s blast furnace tapping channels use ASC castables and repair gunning materials. Some small blast furnace tapping channels use alumina or synthetic mullite-silicon carbide-silicon ramming materials. The tapping channels of blast furnaces in Germany and France generally use ASC ramming materials. France has developed self-flowing castables to increase the service life of the working lining of the main tapping channel.
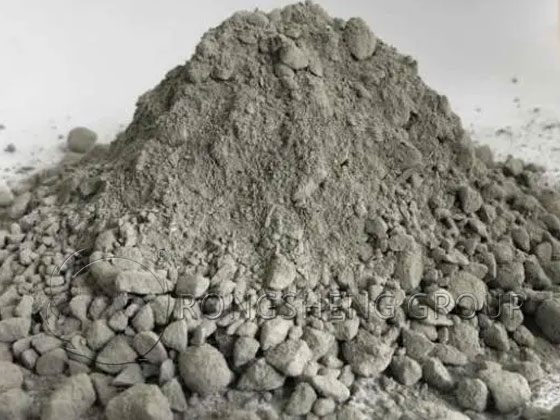
Application of Amorphous Refractory Materials in Aluminum Reverberatory Furnaces
Aluminum reverberatory furnaces are the largest consumers of refractory materials in aluminum plants. The refractory materials used in the furnace have changed from brickwork to integral structures. The refractory materials in contact with the hot metal surface of the furnace are usually acid-bonded plastics, phosphate-bonded bricks, and low-cement castables. The composition of the hot surface refractory materials of the lower side wall is usually the same as that of the furnace, and the insulation materials can be lightweight insulation castables, insulation clay bricks or ceramic fibers. The furnace roof materials are usually high-quality refractory materials such as ramming materials and burning injection materials. The furnace door is usually cast with dense castables or lightweight castables, or a mixture of the two.
Typical Chrome Corundum Castable Lining for Melting Furnace
The melting furnace is operated under intermittent conditions, and the maximum temperature in the furnace is usually 1400~1600℃, and occasionally exceeds 1700℃. In addition, the temperature of the metal layer below the slag line also reaches 1200~1300℃, and all parts of the furnace are high-temperature areas. Therefore, the melting furnace mainly uses ultra-high temperature chrome corundum bricks or chrome corundum castables as furnace linings.
In the actual melting furnace, chrome corundum castables with a Cr2O3 content of 10% are used in parts with relatively mild erosion. Chrome corundum castables with a Cr2O3 content of 20%~30% are used in parts with severe erosion. Chrome corundum castables with a Cr2O3 content of 60% are used in parts such as slag mouths with particularly severe erosion. A typical refractory lining composition diagram for thermal decomposition gasification melting furnace.
About 5% of monoclinic ZrO2 is added to high-chromium Cr2O3-Al2O3 refractories for melting furnaces. The purpose is to improve the thermal shock resistance of the material and extend its service life. Since the structure of the melting furnace is often complex, considering the cost and construction, the melting furnace is mostly built with chrome corundum castables.
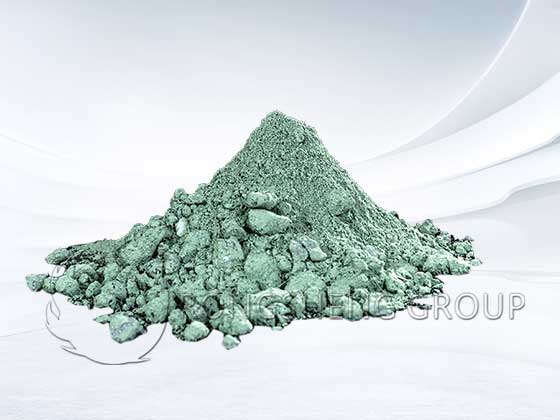
Unshaped Refractory Materials: What is the Difference between High Alumina Clinker and Conventional Cement?
High alumina clinker and conventional cement are two common building materials that are widely used in the construction industry. Although both materials are used in construction projects, there are some differences in their composition, process and use.
First of all, high alumina clinker is a new type of material used in the construction and metallurgical industries. Its main components are alumina and silicate, and it also contains a small amount of elements such as iron, calcium and magnesium. The production process of high alumina clinker is relatively complicated, and it needs to go through multiple process steps such as crushing, mixing, granulation, homogenization, and sintering. This clinker has high strength, high compressive resistance and high refractory performance, and is more stable when used in high temperature environments.
Compared with high alumina clinker, the manufacturing process of conventional cement is relatively simple and the production cost is relatively low. Conventional cement is mainly obtained by mixing raw materials such as cement clinker, gypsum and an appropriate amount of mixed materials. The main components of cement clinker are clinker minerals, which include calcium silicate, ferroaluminate, etc. The strength and durability of cement depend on the composition and production process of the clinker. At present, the main process used is the rotary kiln firing process, which can make the cement clinker reach a high temperature state and promote the formation and crystallization of clinker minerals.
There are also differences in the use of high-alumina bauxite clinker and conventional cement. High-alumina bauxite clinker is generally used in metallurgy, construction, refractory, electricity and other aspects. The main use is as a refractory material in building materials. High-alumina bauxite clinker has high strength, high compressive strength and high refractory performance, and is more stable when used in high temperature environments. Conventional cement is widely used in basic construction fields such as houses, bridges, roads, tunnels, etc.
Rongsheng Monolithic Refractory Manufacturer
In addition, there are some differences between high-alumina clinker and conventional cement in terms of environmental protection. A large amount of waste gas and wastewater will be generated during the production of cement, and the cement industry is also one of the important greenhouse gas emission industries. However, there is less waste gas in the production process of high-alumina clinker, and the discharge of wastewater is not easy to pollute the environment, which belongs to “green building materials”.
In short, high-alumina clinker and conventional cement are both main products in building materials. The production process of high-alumina clinker is complicated, but it can meet the construction needs under special environments. The production cost of conventional cement is relatively low, but its emissions will have a certain impact on the environment. The selection of suitable materials should be based on actual needs and environmental protection requirements.
To purchase high-quality monolithic refractory lining materials, please choose the Rongsheng Manufacturer. Fast production delivery, professional technical R&D team, and product quality are guaranteed. Contact Rongsheng for free samples and quotations.