For a large cement production company, due to a rotary kiln shutdown accident, the 32-hour maintenance and production loss amounted to more than 3 million yuan. This loss, which can easily cost millions, was actually caused by the “red kiln” caused by two silica molybdenum bricks falling off during the firing zone of the rotary kiln. “Red kiln” means that the kiln temperature in a certain area is too high, and if not handled in time, it may cause major accidents such as kiln burnout.
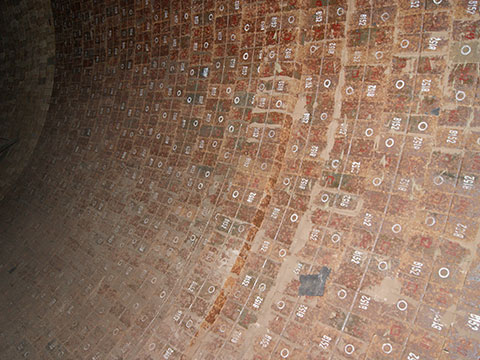
Reasons Why SiC Mullite Bricks Fall Off in Rotary Kiln
The “red kiln” accident was discovered in time. After the kiln was stopped, the staff entered the kiln and found that two sic mullite bricks fell off in the firing zone of the rotary kiln, and a magnesia-alumina spinel brick was twisted at the kiln head. After technical analysis, it was found that there were quality problems with the silica molybdenum bricks and magnesia-alumina spinel bricks used in these two parts. Moreover, during the construction, the construction workers tried to save the trouble and changed the binding agent of the refractory mud without authorization. In the later maintenance, there were also big problems with the maintenance of the staff.
Emergency Repair of Rotary Kiln Head and Firing Zone
After analyzing the above reasons, emergency repair plans for the kiln head and firing zone were arranged respectively.
First, for the silicon mullite bricks in the firing zone, after the kiln was cooled down, all loose and drawn sic mullite bricks in the firing zone were removed and excavation and repair work was carried out. Construction work must be carried out in accordance with construction specifications, and fire clay construction, wooden hammer hammering and wedge iron must be in place. Ensure the normal use of the silica molybdenum bricks there.
In this red kiln accident, in addition to the silica molybdenum bricks, the source of the accident. At the same time, it was also detected that the magnesia-alumina spinel bricks at the kiln head were distorted, and the kiln was shut down for maintenance to deal with them together. The area of distortion here is not large, about 1.5 cubic meters. The same process of digging and filling was adopted. The construction specifications are the same as for the fired zone and must be carried out in accordance with the specifications.
Rongsheng Refractory Materials Manufacturer recommends that when companies build kiln linings if they want to have a long service life, every step and every link must be strictly controlled. The quality of materials, quality of construction and masonry, and post-maintenance must all be taken into consideration in a three-pronged approach. Although the kiln was only shut down for 32 hours for emergency repairs, the company’s losses amounted to millions.
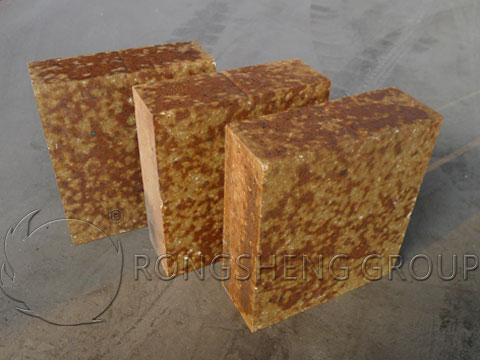
The Influence of the Raw Material Ratio of SiC Mullite Bricks on Their Performance
The main raw materials used in the production of silicon mullite bricks are high alumina bauxite clinker, which is calcined in Shanxi rotary kiln. Brown corundum has high hardness, high melting point, stable chemical properties, and good resistance to acids and alkalis. Silicon carbide, which is synthesized from petroleum coke and SiO2, has a high decomposition temperature and high Mohs hardness. Based on this, choosing corundum and silicon carbide to strengthen the matrix is the prerequisite for the product to have high volume density, high thermal strength, corrosion resistance, and wear resistance. The additive aluminum oxide powder is introduced to improve the high-temperature performance of the product. The binding agent is pulp waste liquid with a density of 1.20-1.25g/cm, and the addition amount is 3%-4%. The chemical composition of the raw materials used is adjusted several times to determine the optimal production process ratio.
The production process is based on the selected materials, and the required raw materials are accurately weighed according to the ratio by adjusting the amount of additives and particles. The particle size composition is based on the principle of “large at both ends and small in the middle”. In order to ensure a uniform matrix, the fine powder is pre-mixed evenly using a spiral mixer to make a mixed powder. Then add aluminum oxide powder, mix the various materials, and put them into the mixing machine. After dry mixing, add sulfurous acid pulp waste liquid and continue mixing evenly. Then, they were pressed into 230mm × 114mm × 65mm standard bricks and 50mm × 50mm cylindrical samples under a 630t press. After drying, they were fired in an electric furnace at 1420°C and kept warm for 3 hours.
The performance testing standards are based on GB/T2997-2000 to detect the apparent porosity and volume density of the fired samples. Test the normal temperature compressive strength of the fired sample in accordance with GB/T5072-1985. According to YB/T376.11-1995, detect the load softening starting temperature of the sample after firing. Test the thermal shock resistance, wear resistance, etc. of the sample after firing.
It can be seen from the experimental results that with the increase of α-alumina powder, the volume density of the sample gradually increases and the apparent porosity gradually decreases. The compressive strength gradually increases, the thermal shock resistance is improved, the wear resistance is significantly enhanced, and the product performance is significantly improved. The main reason is that after the product is fired at 1420°C, the main crystal phases are mullite, silicon carbide, and corundum. The hardness of these crystal phases is very high, which lays the foundation for dense and high-strength refractory products. The addition of α-alumina powder will make the SiO2 in the corundum highly active, which will help to form a denser density in the matrix and significantly increase it. Since AL2O3 and SiO2 form a solid solution, the material grains are refined and densified, and polycrystalline is used to buffer thermal stress. The purpose of improving the thermal shock resistance of the material has been achieved, and the service life of the special sic mullite brick has been greatly improved.