High alumina bricks contain donkey bluestone, which can significantly improve their thermal shock resistance. High alumina bricks containing donkey bluestone. Used in hot blast furnace ceramic burners, cold rolling, continuous annealing furnaces and active lime kilns. In the ceramic industry, it is used as kiln furniture materials and electronic ceramics (Dong Qingshi ceramics). Next, let’s take a look at a coke oven mullite cordierite furnace door tile.
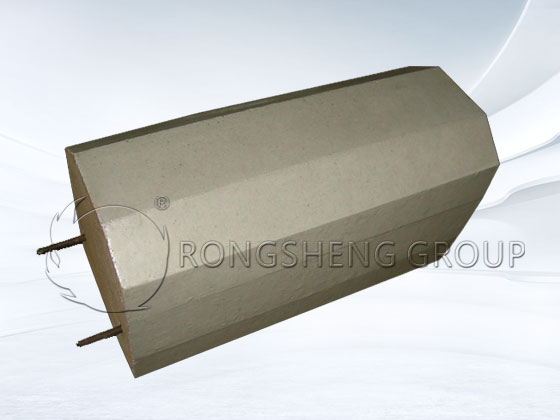
Application of Coke Oven Mullite Cordierite Door Bricks
Coke oven is an important equipment for coking enterprises. Composite ceramic glazed furnace door tiles, with their high strength, anti-wear, anti-erosion and other characteristics, can reduce physical and chemical damage, improve the working environment and environmental protection. Furnace door bricks have excellent thermal shock stability, wear resistance and carbonization resistance. It is made of mullite-cordierite as the basic material and added with composite additives. Improve sealing, save energy and protect the environment, extend service life.
Coke oven is the basic equipment of coking enterprises and is a thermal kiln with complex structure. It is divided into basic roof, small flue, regenerator, chute, combustion chamber, furnace and other parts.
Composite ceramic glazed furnace door tiles are fired with mullite-cordierite as the main crystal phase and composite additives added. The surface is covered with a high-performance microcrystalline ceramic refractory glaze layer, which has high strength, good wear resistance and corrosion resistance. It can reduce physical damage during coke oven operation and the corrosion characteristics of tar and other chemicals on refractory materials.
The new furnace door brick has good sealing performance and does not allow smoke or coke to escape. The high-performance microcrystalline ceramic glaze covered on the surface does not deposit carbon or scorch. It can greatly improve the working environment of workers and reduce environmental pollution.
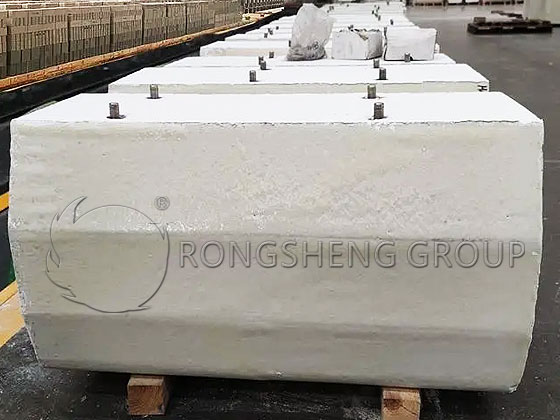
Characteristics of Coke Oven Door Mullite Cordierite Oven Door Bricks
- Low porosity, low thermal expansion rate, and good thermal shock stability.
- Easy to use, the furnace door can be quickly disassembled and assembled, reducing time wasted on maintenance.
- Reduce heat loss caused by loose furnace door sealing and save energy.
- Reduce air pollution caused by loose furnace doors and achieve environmental protection.
Coke oven door lining bricks must withstand harsh temperature conditions. During a working day, the temperature fluctuates between 1000°C and ambient temperature. In addition, it also has to bear the friction with coke when pushing coke, as well as the erosion of ash, slag, moisture and acidic gas, and carbon deposition. This requires the coke oven door lining bricks to have good thermal shock resistance, high temperature volume stability, wear resistance and carbonization resistance.
Cordierite has low thermal expansion and can reach temperatures as high as 1300°C without decomposition and crystal transformation. Consider many aspects such as wear resistance, thermal shock resistance, chemical corrosion resistance, and thermal expansion coefficient. Mullite-cordierite is used as the basic material of the coke oven door brick, which has good thermal shock stability and thermal expansion properties. At the same time, composite micro powder is added as the matrix part, high alumina cement is used as the binder, and composite additives are used. And the anchors are pre-embedded in the product, vibrated into shape, and dried at 450% to make the finished product.
This can not only improve the sealing performance of the coke oven door, prevent smoke from spreading, but also save energy and protect the environment. At the same time, the coke quality is improved and the service life of the furnace door is extended.
Improvement of Bricks Used in Coke Oven Carbonization Chamber and Combustion Chamber
The main refractory material used in coke ovens is silica bricks. However, different parts of the coke oven body have different tasks, temperatures, structural loads, mechanical wear, media erosion, etc. Therefore, in addition to silica bricks, other parts use refractory bricks with different properties. At this time, “three stones” are used.
The work of the carbonization chamber is cyclical, and large temperature fluctuations are its important characteristics. The surface temperature of the furnace wall drops to about 600℃ during coal loading, and rises to 1000~1100℃ at the end of coking. Therefore, the walls and bottom of the carbonization chamber are built with silica bricks. The temperature of the furnace heads at both ends of the carbonization chamber changes suddenly when the furnace door is opened. Silica bricks are no longer suitable for refractory bricks in this area because the temperature limit for silica brick volume stability (573°C) is exceeded. Commonly used are clay bricks. However, clay bricks are easily damaged by long-term thermal shock and are often repaired before other parts, which affects coke oven production. This is a weak link.
In order to solve this problem, a refractory material factory has developed bricks with extremely high thermal shock resistance. Thermal shock stability (1000℃, water cooling) is more than 200 times. This brick has also been used in the coke oven door of a large steel plant. Because the brick is cost-effective, it affects its promotion and application. Later, cordierite bricks were developed, which have excellent volume stability and good thermal shock stability. However, soon after use, it was found that the brick was deformed. The reason was that the low decomposition temperature of cordierite (decomposition at 1460°C) resulted in low refractoriness of the brick.
Due to the application of “three stone” raw materials, low creep sillimanite bricks have been developed and successfully used in large blast furnace hot blast furnaces. Then we developed a series of modified clay bricks and modified high alumina bricks with tristone as the main raw material or auxiliary material. The use effect on coke ovens is better than that of clay bricks and cordierite bricks, with moderate cost performance and is accepted by the market.
To purchase high-quality refractory brick products for coke ovens, please choose Rongsheng refractory brick production and sales manufacturer. We customize refractory lining and refractory brick solutions based on the actual working conditions of high-temperature industrial furnaces. Contact us to get free samples and quotes.