Taking a 100t converter in a factory as an example, the bottom of the converter is ring-shaped masonry. There are 6 fixed air-permeable bricks, and the whole lining adopts a combination of dry and wet masonry (wet masonry is mainly near the tap hole). The construction is carried out by the up-repair method. The simple repairing derrick in the furnace is fixed to the furnace mouth with I-steel, the three-layer construction platform is covered with a bamboo jump board, and the furnace cap is opened for feeding. The construction sequence recommended by the refractory manufacturer is furnace bottom permanent layer→furnace bottom working layer→corner part→furnace body permanent layer→furnace working layer→steel opening→furnace cap permanent layer→furnace cap working layer→furnace mouth.
The construction method of refractory material for integral structure converter
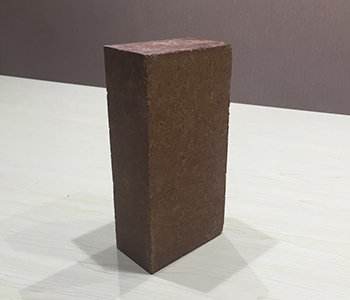
Permanent layer masonry at the bottom of the furnace
Shake the converter to the zero position and lock it, find the centerline of the furnace bottom, check the gas supply sleeve and the pores on the steel structure, and ensure that all pipes and pores are unblocked. Three-layer magnesia bricks are used to build a permanent layer at the bottom of the furnace, laid to the place where the ventilation is left, and rammed with materials close to the furnace shell. The third layer of magnesia bricks is laid to the lower edge of the flange, and the gap between the bricks and the flange is filled with materials.
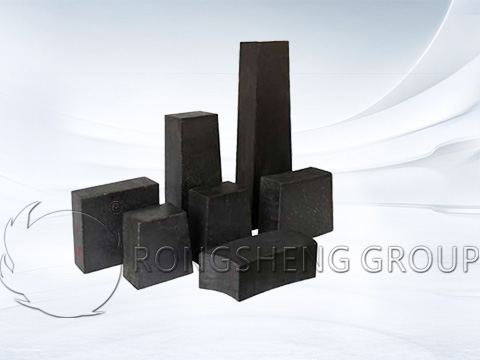
Masonry of furnace bottom working layer
1) The working layer at the bottom of the furnace is erected with magnesia carbon bricks. First, find out the center of the furnace bottom, and build the center bricks according to the pre-assembly. The eccentricity must meet the requirements. The center bricks are built ring by ring according to the design bricks, paying attention to control the wrong teeth. When laying ventilated bricks, the thickness of the brick joints around the ventilated bricks should not be greater than 1mm, and the vent pipe should be bent according to the position of the ventilating duct. After positioning the air-permeable bricks, ram the reserved holes under the air-permeable bricks tightly with materials.
2) When laying the blanks, use the ramming material to control the height of the blanks to ensure the flatness of the upper surface of the blanks. Alcohol resin is used between the blank holder and the permanent layer to be hammered tightly with an air hammer.
3) Permanent layer masonry of the furnace body. The permanent layer of the cone part of the converter melting pool, the straight part of the furnace body, and the cone part of the furnace cap are built with magnesia bricks. Take the furnace shell as the guide surface, close to the furnace shell, adjust the brick closing door, and control the level of each ring. Fill the joints of the bricks with fine magnesia powder.
Masonry of furnace body working layer
1) Magnesia carbon bricks are used to build the cone of the converter bath, the straight tube of the furnace body, and the cone of the furnace cap. With the furnace shell as the guide surface, the working layer is close to the permanent layer, and the expansion joint paper is clamped as required. The gap between the working layer brick and the permanent layer brick is filled with the material to ensure the levelness of each ring. There is one closing door in each ring, and the position of the closing brick is arranged between 15° and 30° from the centerline of the tapping opening. The upper and lower door bricks should be staggered by at least 2 to 3 bricks, and the processing and cutting of the door bricks cannot exceed two-thirds of the original brick width.
2) When the tap hole is built, the position and angle of the tap hole must meet the design requirements. The centerline of the tap hole should be consistent with the centerline of the furnace, and the brine magnesia mortar shall be used for wet masonry. Fill the space between the set brick and the tube brick, between the brick lining and the furnace shell. The expansion joint paper shall not be inserted within 1m of the tapping area, and the brick joint shall not be larger than 1mm.
3) Reserve about 100mm between the uppermost brick of the furnace cap and the furnace door, weld the anchors on the furnace shell, and rammed it tightly with ramming material.
Precautions
The first ring of special-shaped bricks on the furnace body supporting the refractory brick board shall be strictly checked and accepted. The upper and lower surfaces must meet the flatness requirements. Before building the furnace body, carefully check the installation level and firmness of the brick slab. For the masonry of the first ring of special-shaped bricks, use a level to carefully control the level of the upper surface.
Before docking, ensure that the furnace body and the furnace bottom are in a straight position. The surface of the uppermost layer of the furnace bottom is evenly spread on the surface of the bricks. It is required to test the pressure first, and then formally connect after being qualified; the standard is to meet the requirements of the jacking pressure. Then tighten the pin plate, and tamping the butting material from the outside of the furnace with the fire-clay mixture.
For more information on the monolithic refractories for the integral structure furnace lining’s construction, please contact us. We will get you back soon.