Sillimanite bricks are refractory bricks with good characteristics prepared from sillimanite minerals by a high-temperature firing method or slurry casting method. Sillimanite is converted into mullite and free silica after high-temperature calcination. Generally, it is produced by the high-temperature firing method and mud casting method.
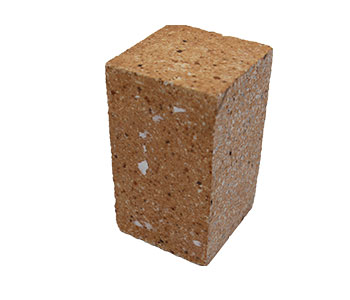
Sillimanite brick is a natural high-grade refractory mineral. It has the characteristics of low thermal expansion, resistance to metallurgical slag and various glass liquids, and good high temperature wear resistance. Its physical and chemical properties are better than high alumina bricks, with refractoriness of 1770~1830℃, and the starting point of load softening at 1500~1650℃. It is mainly used for the forming of the flow hole of the glass tank kiln, the lining of the blast furnace, the throat, and the ceramic industrial kiln furniture. Refractories based on natural sillimanite also have these advantages. Therefore, sillimanite refractories are widely used in metallurgy, chemical, and building materials industries.
The application of anti-stripping sillimanite brick in the regenerator of a glass melting furnace. The manufacturing process and performance raw materials: special grade bauxite clinker: 3-0mm55%. Sillimanite fine powder: 0.246-0.043mm25%-35%. Combined clay powder: 0.088~0.024mm5%~8%. Physical and chemical properties, the softening temperature under load is 1550℃. Compressive strength at room temperature is 126MPa. The bulk density is 2.75g·cm-3. The linear change rate of reheating (1450℃, 2h) 0.2%. The apparent porosity is 20%, etc.
Sillimanite bricks for blast furnaces. Research has been carried out on the apparent porosity and thermal shock stability of sillimanite bricks. The sillimanite brick sintered with sillimanite as the main raw material can satisfy the stability and tightness of the blast furnace tuyere.
Application of anti-stripping sillimanite bricks in regenerator of float glass melting furnace. Low-porosity clay bricks are often used in the lower lattice body of the regenerator of the glass melting furnace. Anti-stripping high alumina brick destruction mechanism, research, and development of anti-stripping silicon wire brick. Through trials, it is a new material suitable for the grid body of the regenerator, which is corrosion-resistant, does not hang slag, and extends the service life.
Production and use of sillimanite bricks for steel-making electric furnace roof. The average speed of sillimanite bricks produced with sillimanite as the main raw material is 2.639mm per furnace. This is 31.8% lower than that of the high alumina brick on the top of the electric furnace. The average number of rapid cooling and rapid heating per unit loss thickness is 1.216 times/mm for sillimanite bricks and 0.827 times/mm for high alumina bricks on the top of the electric furnace. The sillimanite brick used for the top of the steel-making electric furnace can significantly increase the service life of the electric furnace cover.
Production Process and Control of Sillimanite Bricks
First, select qualified raw materials. These include natural sillimanite, synthetic mullite, high-alumina clinker, kaolin, etc. At the same time, a plaster mold is made according to the shape of the product, and a binder electrolyte is prepared, and then the slurry required for casting is prepared.
Formed. Pour qualified mud slowly into the mold, spread the mudflat when it is full, and cover with gypsum board (upper template). Then demould, demoulding time depends on the thickness of the blank. After the rough blank is formed, the inside and outside must be trimmed, that is, the blank is trimmed. The formed semi-finished products must be dried to a certain level of moisture, then loaded into the kiln and fired at high temperature to become finished products. After the neck processing, product inspection, packaging, and leaving the factory.
After adding sillimanite and andalusite to high alumina bricks, the product has good volume stability. When w(Al2O3)=75%~80% in the low creep high alumina brick, the high alumina brick has the best structure and performance. Using bauxite, bauxite corundum, sillimanite, and clay as raw materials, high creep resistance high alumina bricks for hot blast stoves have been developed. The high-alumina brick is applied to a large-scale steel company, and the results show that the use of the low-creep high-alumina brick in a hot blast stove can increase the air volume and increase the air temperature. Achieve the effect of reducing the coke ratio, saving energy, increasing the utilization factor of high protection, and producing more iron.