Compared with iron and steel smelting, the smelting of non-ferrous metals has complex processes and long processes. There are many types of furnaces used for smelting and many types of refractory materials are used. In terms of usage, the most commonly used are magnesia bricks, magnesia chrome bricks, clay bricks, high alumina refractory bricks, carbon materials, etc.
Copper Production Process
The copper production process consists of five parts: pre-smelting treatment, matte smelting, blister copper blowing, fire refining, and electrolytic refining. Copper concentrates are mainly sulfide ores and oxide ores, with very little natural copper. Two-thirds of it is sulfide ore, which is symbiotic with iron ore and accompanied by a variety of valuable metals. Therefore, while extracting copper, valuable metals must be recovered and comprehensively utilized.
Copper smelting uses many high-temperature furnaces, and the material properties change greatly during the smelting process. The selection of refractory materials is also different. The following is only a typical introduction.
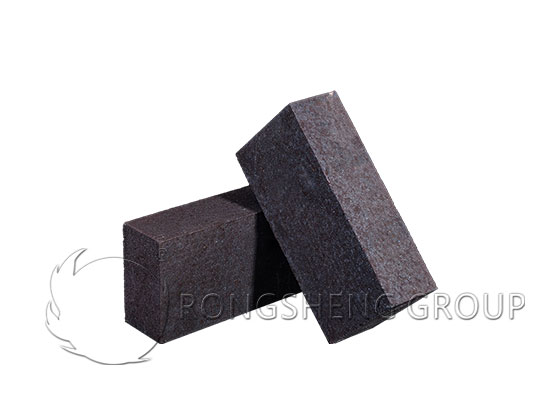
Refractory Materials for Converter Copper Smelting
In the process of copper smelting, matte is made into blister copper, using the converter blowing method. Matte converters are divided into three types: horizontal, vertical and cylindrical. At present, most countries around the world use horizontal converters. There are many specifications and models of horizontal converters, but PS-type side-blown converters are commonly used, and medium and large sizes are the main ones.
The process of blowing matte in a converter to produce blister copper is divided into two cycles. The first cycle starts from loading matte and adding quartz sand to make slag until the slag is poured out, which is called the slag-making period. If there are many impurities, the operation must be repeated several times. The slagging reaction is a violent exothermic reaction, and the furnace temperature rises very quickly. Excessively high furnace temperature will accelerate slag corrosion and furnace lining melting loss. Therefore, at the end of slagging, a certain amount of cold material must be added to cool down. The second cycle is after pouring the slag and blowing continuously until all S in Cu:S is removed. When the copper content in the blister copper reaches more than 99%, the blowing is completed, the blowing is stopped, and the copper is produced. Converter blowing is an intermittent operation, and the furnace temperature is as high as 1450°C or above. After copper is extracted, the temperature of the empty furnace wall is about 600-700°C. During this period, the temperature suddenly changed violently, causing the furnace lining to crack and peel off. In addition, the furnace lining is severely chemically corroded by high-temperature molten slag, and the slag line area is particularly prominent. Under the action of external force (blast), the melt is violently stirred, and the influence of the rotation of the furnace intensifies the erosion of the slag on the furnace lining. Therefore, the converter lining often suffers from melting loss, peeling, cracking, and brick loss. It is required to use high-quality refractory materials with high refractoriness, high volume density, low porosity, good slag resistance, and good thermal shock resistance. When laying bricks, the joints should be small and the surface should be smooth. When partial damage occurs, it must be repaired in time.
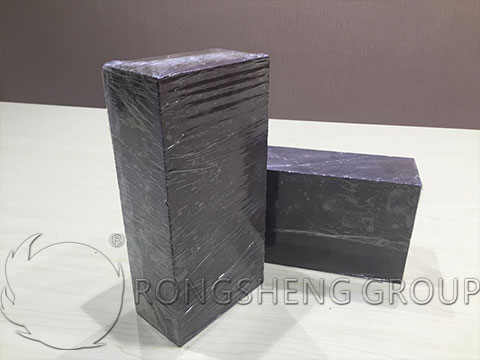
The refractory materials used in converters are roughly the same in each factory. On the layer next to the steel furnace shell, a permanent lining is made with brine combined with magnesia refractory ramming material, with a thickness of 50-100mm. Then lay the working lining of magnesia bricks or magnesia chrome bricks with a thickness of 300-500mm. The lining of the tuyere area and slag line area is very easy to be damaged and is the weak link of the converter. Directly bonded magnesia-chromium bricks or fused-cast magnesia-chromium bricks are generally used. Some foreign countries use magnesia bricks made of fused magnesia, magnesia-chromium bricks made of fused magnesia-chromium particles, fused-cast magnesia-chromium bricks with a MgO content of 70%, magnesia spinel bricks and calcium oxide bricks, which have good results.
The converter lining life is short and the unit consumption of refractory materials is high. Blowing 1 ton of blister copper consumes 11kg of magnesia bricks and 3kg of magnesia-chrome bricks. To extend the life of the furnace, in addition to using high-quality refractory materials, the main thing is to strictly enforce the operating system and thermal system. The newly built furnace lining or the overhauled furnace lining is first strictly baked. After reaching the specified temperature, it is directly filled with matte and blown directly without adding a slagging agent. To form a large amount of Fe2O3 and other substances, let them adhere to the surface of the furnace lining, hang slag skin, and form a protective layer before it can be put into normal blowing. Otherwise, magnesia-chromium bricks will be difficult to withstand the strong erosion of molten slag and will be easily damaged.
Direct Bonded Magnesia Chromium Bricks for Converters
At present, the most widely used technology in converters is directly bonded magnesia-chromium bricks. The furnace body is built with directly bonded magnesia-chromium bricks, and the converter lining is built with electrofusion and then bonded magnesia-chromium bricks to build the tuyere, furnace mouth, and other positions. application. Take the lining construction of a 150t copper converter in a certain factory as an example. Ordinary silicate-bonded magnesia-chromium bricks are used to build the cylinder and end wall lining, and direct-bonded magnesia-chromium bricks with high chromium content are used to build the tubes and linings of the tuyere slag lines with serious erosion, which has achieved good results. Another copper plant used improved electrofusion combined with magnesia-chromium bricks to build tuyere and achieved good results, extending the furnace life and reducing the period of minor repairs.
Generally speaking, ordinary magnesia-chromium bricks are currently used to build the furnace lining, and directly bonded bricks or electro-fused magnesia-chromium bricks are used to build the tuyere, slag line, furnace mouth, and other positions as the general method for lining the copper converter. RS Refractory Brick Manufacturer is a powerful manufacturer and seller of refractory bricks. We have many use cases of magnesia-chromium bricks. To purchase high-quality magnesia bricks and magnesia-chrome bricks for converters, please contact us.