Brief introduction of fused zirconia mullite bricks. By introducing ZrO2 into Al2O3-SiO2 bricks to improve the structure of mullite, the chemical corrosion resistance, thermal shock resistance and expansion coefficient of mullite can be improved. Therefore, this kind of mullite brick containing ZrO2 is commonly called zirconium mullite brick. It is generally made by the electric melting method, which is called fused zirconium mullite brick. It is also produced by the sintering method, which is called sintered zircon mullite brick.
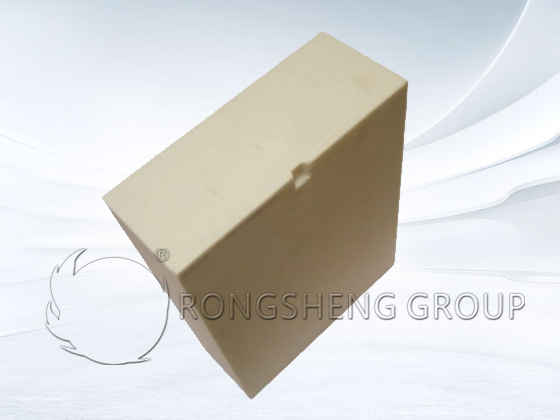
Properties of Fused Zirconia Corundum Bricks
Fused zirconia-mullite bricks are usually made by adding zro2 to aluminum-silicon refractory bricks such as high-alumina bricks, and then made by electrofusion. The most obvious is that the chemical corrosion resistance and thermal shock resistance of mullite in fused zirconia corundum brick products have been significantly improved, and the expansion coefficient has also been reduced.
Sintered zircon mullite bricks are made of industrial alumina and zircon concentrates as raw materials. The zirconia-mullite brick refractory material is made by introducing zirconia into the mullite matrix through the reaction sintering process.
The introduction of zirconia into mullite bricks can greatly improve the high-temperature mechanical properties of mullite materials by using the phase transformation toughening of zirconia. Zirconia can promote the sintering of mullite materials. The addition of ZrO2 can accelerate the densification and sintering process of ZTM materials due to the generation of low melting point substances and the formation of vacancies. When the mass fraction of ZrO2 is 30%, the relative theoretical density of the body fired at 1530°C reaches 98%, the strength reaches 378MPa, and the toughness reaches 4.3MPa·m1/2.
Using industrial alumina and zircon as raw materials, the zircon mullite bricks made by reaction sintering are difficult to control the process because the reaction and sintering are carried out at the same time. Usually, when firing, it is first kept at 1450°C to make it densified, and then the temperature is raised to 1600°C for reaction. ZrSiO4 decomposes into ZrO2 and SiO2 at greater than 1535°C, where SiO2 and Al2O3 react to form mullite. Since a part of the liquid phase appears when ZrSiO4 is decomposed, the decomposition of ZrSiO4 can refine the particles and increase the specific surface area, thereby promoting sintering.
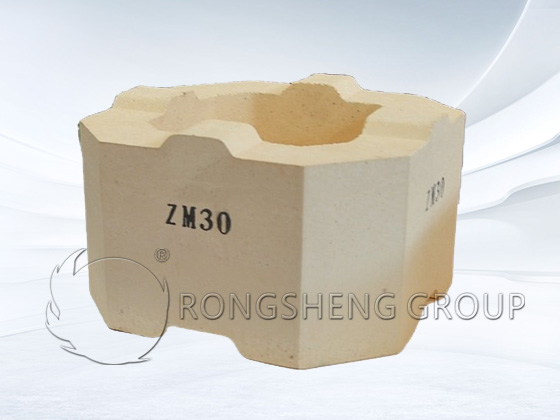
Studies have shown that when the amount of zircon added is less than 54.7%. With the addition of zircon, the microstructure of the sintered sample gradually transitions from the network structure of columnar corundum to the network structure of columnar mullite. The high-temperature flexural strength of the sample (at 1400°C) also increases with the increase of zirconia content. A larger value appears when the zirconia content is 23.7%, and then the strength decreases. The addition of zircon contributes to the improvement of thermal shock resistance.
Physical and Chemical Indicators of Fused Zirconia Mullite Series
Items | 75 Mullite brick | 70 Mullite brick | 65 Sillimanite brick | 60 Sillimanite brick | 55 Sillimanite brick | Andalusite Brick |
AL2O3% | ≥75 | ≥70 | ≥65 | ≥60 | ≥55 | ≥53 |
SiO2% | ≤23 | ≤25 | ≤32 | ≤37 | ≤42 | - |
Fe2O3% | ≤0.5 | ≤0.8 | ≤1.0 | ≤1 | ≤1.5 | ≤1.7 |
TiO2% | - | - | - | - | - | ≤0.6 |
K2O+Na2O% | - | - | - | - | - | ≤0.6 |
Bulk density (g/cm3) | ≥2.7 | ≥2.6 | ≥2.5 | ≥2.3 | ≥2.3 | ≥2.4 |
Apparent porosity (%) | ≤18 | ≤18 | ≤18 | ≤19 | ≤20 | ≤20 |
Cold Crushing Strength (MPa) | ≥80 | ≥65 | ≥60 | ≥60 | ≥50 | ≥60 |
Refractoriness Under Load ℃(0.2MPa ,0.6%) | ≥1680 | ≥1680 | ≥1650 | ≥1600 | ≥1580 | ≥1600 |
This series of products are mainly used for the lining of various parts of thermal kilns in steel, chemical, glass, ceramics, and other industrial sectors. |
Raw materials for Fused Zirconia Mullite Brick
Fused zircon mullite is made by melting high-purity alumina and zircon sand in an electric arc furnace. Through smelting, zircon sand and alumina react to form a mixture of mullite and zircon sand. It is an ideal product for special materials that require high environmental corrosion resistance and a low thermal expansion coefficient. Can be widely used in cast ceramic pressure pipes and refractory-shaped products (resistant to slag and molten glass at high temperatures). The Zircon mullite bricks made are used in the glass industry and also as additives for continuous casting refractory materials.
Rongsheng Fused Zirconia Mullite Brick Manufacturer
Rongsheng refractory brick manufacturer is a refractory brick manufacturer with rich production and sales experience. Our refractory products have been sold to more than 100 countries and regions all over the world. Our refractory brick products have reliable product quality, long service life, and low purchase cost. Contact us for free price and refractory brick-lining solutions.