Fused casting refractory materials for glass kilns. On the one hand, fused casting is less restricted by molds, which makes it easier to manufacture large products and helps reduce erosion in and along brick joints. On the other hand, the apparent porosity of fused casting materials is very low, and it is difficult for molten glass to penetrate into the material. Therefore, fused casting materials have incomparable erosion resistance compared to ordinary sintered refractory materials. However, the erosion resistance of different fused refractory materials is still very different, and refractory materials should be used reasonably according to the location of the kiln and the material properties.
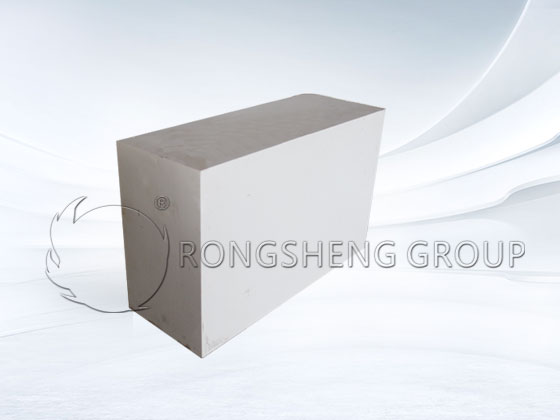
Performance and Use Location of Fused-Cast Refractory Materials
Figure 1 shows the erosion rate of different fused-cast refractory materials in Na2O-CaO-SiO2 glass liquid at different temperatures after 95 h of testing. As can be seen from Figure 1, below 1400 ℃, the erosion rate of each fused-cast material is very small. Above 1400 ℃, the order of erosion resistance is: Cr2O3-Al2O3, 41# AZS, 36# AZS, 32# AZS, α-Al2O3, α-β-Al2O3. Due to the coloring of Cr2O3, the melting part of the glass furnace is built with 33#, 36# and 41# fused-cast AZS bricks.
Usually, 41# fused-cast AZS is used for harsh locations, 36# fused-cast AZS is used for medium-erosion locations, and 33# fused-cast AZS is used for relatively mild locations. The breast wall of the cooling part can be made of β-Al2O3 bricks, and the pool wall and bottom bricks of the cooling part can be made of α-β-Al2O3 fused-cast bricks. In recent years, domestic and foreign manufacturers, especially foreign companies, have greatly increased the ZrO2 content of fused-cast zirconium corundum materials, such as increasing the ZrO2 content of 33# AZS to 34% ~ 35% (w), the ZrO2 content of 36# AZS to 37% ~ 39% (w), and the ZrO2 content of 41# AZS to 43% ~ 45% (w).
Relationship between the Composition, Structure and Properties of Fused-Cast Zircon Corundum Materials
Conclusions drawn from the experiment:
- (1) Increasing the content of Na2O and SiO2 increases the amount of primary baddeleyite, reduces the amount of aluminum-zircon eutectoid, and increases the amount of matrix (1.35×1.06-1.07>0). This is because increasing the content of Na2O and SiO2 increases the content of glass phase and improves the ability of glass phase to dissolve Al2O3.
- (2) Primary baddeleyite has little effect on the corrosion resistance of fused-cast AZS refractory materials (the coefficient is -0.02). On the one hand, the increase of primary baddeleyite leads to an increase in glass phase and a decrease in corrosion resistance; on the other hand, primary baddeleyite limits the loss of glass phase, offsetting some of the adverse effects caused by the increase of Na2O and SiO2.
- (3) Increasing the SiO2 content or reducing the Na2O content increases the viscosity of the glass phase, making it difficult to remove pores and increasing the true porosity.
- (4) When heated, the pores can accommodate a certain amount of glass phase, reducing the seepage of the glass phase and thus increasing the initial precipitation temperature of the glass phase.
In the fused-cast zirconium corundum material, zirconium oxide has the function of improving corrosion resistance. The glass phase helps melting when melting, and relaxes thermal stress and reduces the harm of zirconium oxide phase transformation when cooling. The key point of the process of fused-cast zirconium corundum refractory is to make the primary baddeleyite with suitable particle size and shape evenly distributed in the glass phase with suitable composition and quantity. Make the primary baddeleyite and the glass phase cooperate with each other and protect each other. This can make the fused-cast corundum refractory have a higher zirconium oxide content, a lower glass phase content and a higher manufacturing qualification rate. To this end, it is necessary to improve the automation level of the equipment and optimize the molding, melting, casting and annealing processes.
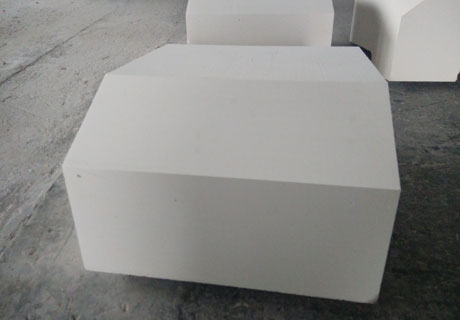
New Varieties of Fused-Cast Refractory Materials
With the promotion of the full oxygen combustion process, the concentration of alkali vapor in the flame space of the glass kiln has increased greatly, seriously corroding the refractory materials in the upper space of the glass kiln. The corroded refractory materials enter the glass liquid in the kiln, producing stones, streaks and bubbles, affecting the quality of the glass. Therefore, low-leakage fused-cast refractory materials have been developed, and their performance indicators are shown in Table 1.
As can be seen from Table 1, the Na2O content in 36# AZS is 0.4% (w) lower than that of 33# AZS, so the glass phase content is reduced from 21% to 14% (w). This means that more expensive desiliconized zirconium must be added to the ingredients, the melting temperature must be increased during melting, and the cooling rate of the bricks must be controlled during cooling. These measures significantly increased production costs, but the glass phase bleedout was only reduced from 1.5% to 0.7% (w). The completely opposite technical route is adopted, which greatly reduces the content of ZrO2, increases the content of Al2O3, and especially increases the content of Na2O. Since the content of ZrO2 dropped from 33% to 17% (w), the manufacturing cost was greatly reduced; the amount of glass phase bleeding was reduced from 1.5% (w) to 0, which greatly improved the anti-bleeding performance.
According to the Al2O3-SiO2-ZrO2 ternary phase diagram, when cooling, ER2001 first precipitates corundum, and then precipitates corundum and mullite at the corundum-mullite connection. However, due to the high Na2O content, only corundum precipitates. Finally, corundum and baddeleyite precipitate at the lowest eutectic point. Due to incomplete crystallization of zirconia, the remaining zirconia can increase the viscosity of the glass phase. Since fine baddeleyites are distributed in the glass phase, the flow of the glass phase is restricted. Therefore, the amount of glass phase bleeding is zero.
New Molding Process for Fused-Cast Refractory Materials
Recently, domestic fused-cast refractory manufacturers have transplanted the technology of the casting industry to improve the manufacturing level of fused-cast refractory materials. Such as resin sand, investment mold, lost foam and V-method casting.
Resin sand uses phenolic resin or furan resin as a binder. For example, the original sand is mixed with thermoplastic phenolic resin, urotropine, calcium stearate, etc. to make coated sand, which is molded and heat-treated to form a model. The advantages of resin sand molding are: high production efficiency, high model strength, high model accuracy, and few surface defects of castings; the disadvantages are: high resin price and environmental pollution. Investment casting and lost foam casting are suitable for manufacturing special-shaped fused-cast materials.
Investment casting is also called “lost wax casting”: paraffin is made into castings, refractory materials are applied on the outside, and the paraffin is poured out after solidification and heating, and then heat-treated to make a model.
When losing foam casting, use foam plastic to make a mold, dip-coat it with refractory material and put it into a vacuum-able sand box. Fill the foam plastic with molding sand and tap it, then cover it with plastic film and vacuum it. During casting, the foam plastic vaporizes rapidly when heated, the vaporized material is removed, and the melt forms a refractory material after cooling. Because the melt contacts the plastic during casting, lost foam is not suitable for manufacturing oxidized zirconium corundum materials.
The V method is a molding method named after the initials of Vacuum, which is a vacuum sealing molding method. The V method was born in Japan in the late 1960s and was introduced to China in 1974. At present, hundreds of foundries in my country use the V method for production. Advantages of the V method: 1) The surface precision of castings is high; 2) The processing margin of castings is small, which is beneficial to saving processing time, power consumption and material consumption; 3) It saves raw materials and labor costs, and the recovery rate of molding sand can reach 95%. And the man-hour consumption is about 60% of that of wet molding; 4) Since the gases generated during molding and casting are taken away by the vacuum pump, there is less pollution and the working environment is improved.