Before producing high alumina bricks, high alumina brick slurry must be prepared. Rongsheng high alumina brick manufacturer. High alumina brick slurry is prepared in a slurry mixer, the slurry density is 1.5~1.65g/cm³, the temperature is 50~70℃, and the mud is prepared in a wet mill.
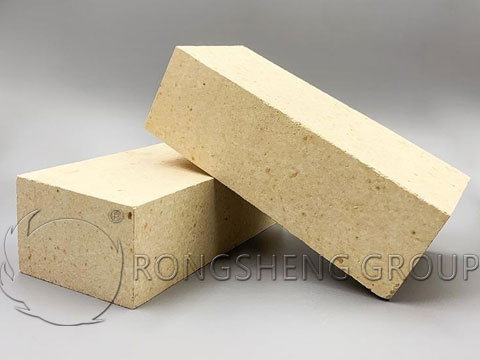
Preparation Procedure of High Alumina Bricks
The preparation procedure of high alumina bricks is as follows: first unload the cone material into the wet mill according to the proportion of ingredients, add clay slurry and sulfite pulp waste liquid, mix for 2~3min, then add the drum mill powder, and mix for another 10~20min.
The moisture content of the slurry should meet the following requirements: 5.5~6.5% for general high alumina bricks, 5.3~5.8% for blast furnace high alumina bricks. 9.2~9.7% for hand-formed high alumina bricks with a unit weight greater than 60Kg, and 9.7~10.2% for high alumina bricks less than 60Kg. 6.1~6.6% for high alumina bricks with a wind hammer forming height greater than 200mm, and 6.8~7.3% for high alumina bricks with a height less than 200mm.
After mixing the mud, the material should be trapped. Trapping conditions: temperature 15~30℃, relative humidity above 80%, and time not less than 20h. The material should be covered during the trapping period to reduce water evaporation. In this way, after the mud needed for the production of high alumina bricks is prepared, the mechanism stage begins. The porosity of the body of the machine-formed high alumina bricks must be controlled.
In order to reduce the porosity of high-alumina bricks and improve the quality of high-alumina bricks, the molding pressure must be increased. For ordinary high-alumina bricks, the molding pressure should reach 600MPa. The molding pressure of high-density high-alumina bricks should be above 600MPa. In other words, only by using a hydraulic press above 600MPa can such an effect be achieved. The porosity of high-alumina brick blanks should meet the following requirements: I-level high-alumina bricks ≤21%, II-level high-alumina bricks ≤23%, III-level high-alumina bricks ≤22%. Before molding, check the model size. The scale rate of ordinary high-alumina brick models is 1.5% on the upper part, 3.0% on the middle and lower pressure surfaces, and 1.5% on the non-pressure surface.
Strictly select raw materials and produce high-quality high-alumina brick products according to the production process. Rongsheng manufacturer, reliable product quality, guaranteed customer service.
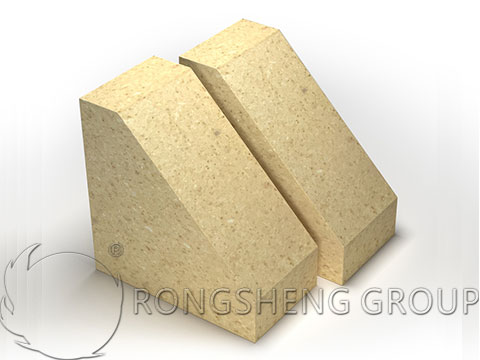
Why do High-Alumina Bricks Used in Furnaces Crack?
In addition to slag erosion, the reason why high-alumina bricks are damaged during use is that the rapid change in temperature causes cracks and spalling. So, why do high-alumina bricks crack when they are fired above 1000℃?
It is caused by rapid cooling wind and alternating hot and cold. Because of the influence of wind, rapid cooling and heating, the thermal shock stability of high-alumina bricks is destroyed, so cracks will appear. In severe cases, there will be spalling, that is, high-alumina bricks fall down in blocks.
The thermal shock resistance of high-alumina bricks is water-cooled at 850℃, and the cycle is only 35 times. This is due to thermal expansion and no crystal transformation. If the lining is heated to a high temperature during use, and then quickly cooled down and repeatedly heated and cooled sharply. It will seriously affect the thermal shock stability of high-alumina bricks.
High alumina bricks have different grades and qualities. Heat the temperature to 900℃, then put it into cold water, and repeatedly heat and cool it rapidly. When cracks appear on the surface of the refractory brick or the surface falls off, the weight loss will reach 20% of the high alumina brick. Of course, the rapid cooling and heating that high alumina bricks can withstand cannot be used as an indicator of rapid cooling and heating resistance. Because the actual use conditions of high alumina bricks are completely different, the test results can only be used as a comparison of the rapid cooling and heating resistance of refractory bricks of different grades.
During the use of high alumina bricks, they often encounter rapid changes in temperature. The ability of high alumina bricks to withstand rapid changes in temperature is called thermal stability. Therefore, improving the performance of high alumina bricks in resisting rapid cooling and heating is also one of the most important measures to extend the service life of refractory bricks.
During use, when cracks appear on high alumina bricks due to alternating hot and cold, the material of the refractory bricks can be changed according to the characteristics of the fired products. To meet the needs of special parts. But the material of the refractory bricks must be changed according to the temperature, erosion, and gas field.

What Will High-Alumina Bricks Look Like After being Corroded?
There are iron oxide components in high-alumina bricks, and iron will produce liquid phase during the sintering process of high-alumina bricks. If the content is too high, it will affect the service life of high-alumina bricks during use.
After high-alumina bricks are corroded in the furnace, the structure will change. Due to the melting of iron oxide, more agglomerates will appear on the edge of the pores. Iron oxide melts out of the crystal and will be distributed on the surface of the crystal. The mullite crystals in the high-alumina bricks are damaged. The most intuitive thing to see is that many small holes appear on the surface of the high-alumina bricks. As the use cycle lengthens, the holes will become larger and larger, and the erosion area will become larger and larger, affecting the use of high-alumina bricks.
After the high-alumina bricks are corroded, the corrosion of iron oxide during heating causes iron to dissolve out of mullite, and also causes large-scale damage to the mullite structure. Every time it is heated, there will be more and more cracks on the surface of the high-alumina bricks. And the strength of the high-alumina bricks after corrosion is also greatly reduced.
The strength of high-alumina bricks decreases, and the load-bearing and erosion capacity also decreases, and the service life will also decrease. As the area of iron oxide on the surface of high-alumina bricks increases, the pores become larger and larger, and the area of corrosion will become larger and larger, which will exit the service cycle very early, and new high-alumina bricks will be replaced to adapt to the use of kiln linings.
After being corroded, high-alumina bricks will also have blackheads, cracks, and fractures that can be seen at a glance. If they are not replaced in time, it will affect the deformation of the kiln lining from the inside to the outside. So that it will affect the construction when the high-alumina bricks are replaced next time, which will also bring a lot of inconvenience. Because the furnace shell is affected, even if the high-alumina bricks are replaced, it is very easy to cause falling off, which will eventually affect the service life.
Therefore, when the kiln lining uses high-alumina bricks or refractory bricks of other materials, it is necessary to select the most used material according to the erosion of the kiln lining for long-term use of the kiln lining. That is, it saves the replacement frequency and reduces unnecessary expenses.
To purchase high-alumina brick products, please choose Rongsheng manufacturers. Customized size and shape. Contact Rongsheng manufacturers for free quotes.