Low cement series refractory castables are developed on the basis of clay combined with refractory castables. Its main varieties include low cement, ultra-low cement, and cement-free refractory castables. It combines the advantages of most refractory castables and has the characteristics of high density, low porosity, high strength, earthquake resistance, and erosion resistance. Low cement refractory castables are mainly defined and classified based on the CaO content in the castables. Because almost all of the CaO in refractory castables comes from the cement binder, the formulation of low-cement castables limits the amount of aluminate cement used.
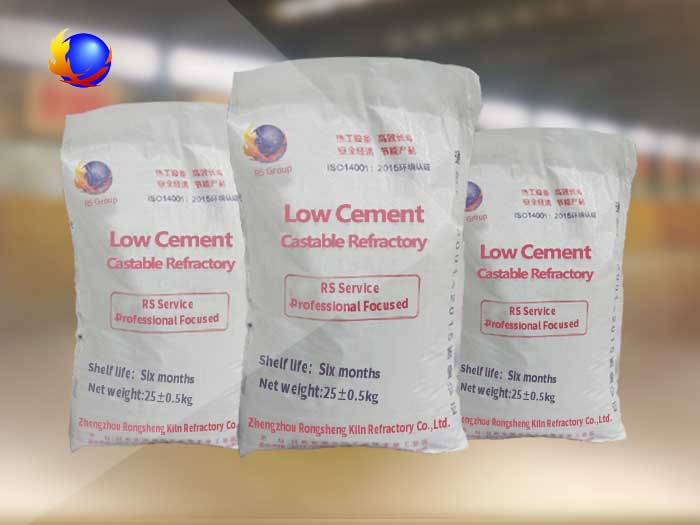
Configuration Guide for Low Cement Series Refractory Castables
When preparing low-cement refractory castables, it is necessary to reasonably select the particle gradation, micro powder, and additive types and dosages. Refractory aggregates and powders are made from clay clinker and high alumina bauxite clinker. Generally speaking, when configuring low-cement refractory castables, it is necessary to use three or four levels of grading to achieve the maximum bulk density. The dosage of refractory aggregate is generally 65%-75%. The maximum particle size of the aggregate is mainly determined by the thickness of the casting lining, which is generally 10mm. Its particle gradation: 10-5mm (30%-40%); 5-3mm (20%-30%); 3-0.1mm (30%-40%).
Refractory powder generally uses special-grade high-alumina bauxite as raw material, and undergoes iron removal treatment after grinding. The fineness less than 0.05mm should be greater than 90%. Sometimes high-end materials such as alumina powder and corundum powder of the same fineness need to be added according to the requirements of working conditions. The dosage of refractory powder is generally 20%-25%.
There are many varieties of refractory ultrafine powder, and silica fume (SiO2 powder) is commonly used. Sometimes other fine powders are added, and the dosage is generally about 3%-10%. Different varieties of low-cement refractory castables have different dosages of ultrafine powder, and each has a corresponding optimal dosage, which needs to be determined through experiments.
In low-cement refractory castables, the admixtures used mainly include high-efficiency water-reducing admixtures and dispersants. Its varieties include humic acid, citric acid, SM, NNO, MF, etc. and their salts, sodium tripolyphosphate, sodium hexametaphosphate and boric acid, etc. The dosage is generally 0.03%-1.0%. Generally speaking, the water reduction rate and dispersion effect of organic additives are better than those of inorganic additives. In addition, a small amount of expansion agents such as andalusite, kyanite, and sillimanite are also added. Make it slightly expand at high temperatures.
Once you are familiar with these basic principles of preparation, you can prepare various types of low-cement castables. For example, use 70% of first-grade bauxite clinker aggregate of 8-0mm and 20% of same-grade bauxite clinker powder. No. 625 CA-50 cement 5%, silica fume 5%. A castable made of 0.2% sodium tripolyphosphate and 6.5% water can be made into a better low-cement refractory castable.
The 3 Different Low-Cement Refractory Castables
(1) Low Cement Aluminum Silicate Refractory Castable
Low-cement aluminum silicate refractory castables use first-grade clay clinker and first-grade to special-grade alumina clinker as aggregates. Generally, the maximum particle size is 10mm and the dosage is 70%. Refractory powder is made of special grade or first-grade bauxite clinker powder or brown corundum powder, etc., and its dosage is 18% to 24%. Ultrafine powder uses α-Al2O3 powder and silica fume, the dosage is 6%~12%. Add an appropriate amount of compound water-reducing agent.
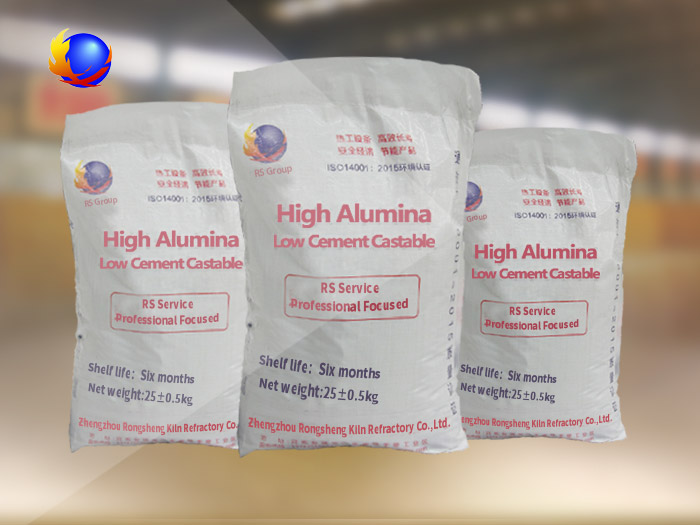
Performance Advantages of Low Cement Aluminum Silicate Refractory Castables
The refractory degree of low cement refractory castable is greater than 1790℃. The load softening temperature under 0.2MPa (deformation 4%) is 20~100℃ higher than that of CA-50 cement refractory castable. Therefore, the service temperature of low-cement refractory castables is generally about 100°C higher than that of CA-50 cement refractory castables of the same material.
The high strength and medium-temperature strength of low-cement refractory castables do not decrease but increase significantly. There are many reasons for this.
Among them, the dehydration of calcium aluminate hydrate is carried out slowly and continuously within a large temperature range. And less damage to the crystal structure.
Low-cement refractory castables have less total pores, more small capillary pores and even distribution. That is, it has the characteristics of low pores, good pore structure, poor air permeability and strong resistance to slag erosion. This is also one of the reasons for the high strength of this castable.
Due to the low apparent porosity of low-cement refractory castables, the structure is dense. Therefore, it has high strength at medium and high temperatures.
Low cement refractory castables have high strength, good wear resistance, low apparent porosity and few low melting point materials. Therefore, it has strong resistance to slag invasion.
The thermal shock resistance of low cement refractory castables, that is, the number of cycles of water cooling after heating to 1100°C, is the same as that of CA-50 cement and clay combined refractory castables. are more than 15 times. Its thermal conductivity is slightly higher than that of CA-50 cement and clay combined refractory castables due to its low pores and dense structure. Its value is generally 1.05~1.35W/(m·K).
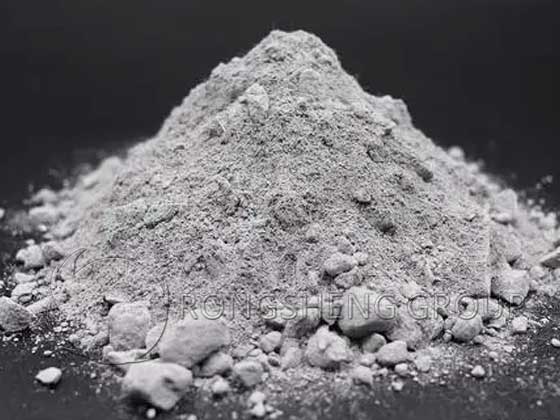
(2) Low Cement Mullite Corundum Castables
Low cement mullite corundum refractory castables use sintered or electric fused mullite, brown corundum, alumina-based corundum and white corundum as refractory bone powder. Sometimes special-grade alumina clinker powder is also used, and ultra-fine powder is mixed with α-AI2O3 and silica fume. It is formulated with aluminate cement as binder and additional dispersant. This material is used for steel rolling heating furnace lining, water cooling pipe wrapping and burner bricks, and tundish slag weir. On thermal equipment such as tap troughs and electric furnace covers of medium and small blast furnaces. The use effect is better.
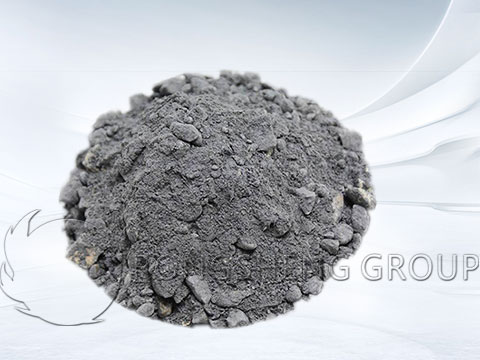
(3) Low Cement SiC Refractory Castable
Low cement SiC refractory castables are characterized by low linear expansion coefficient, high thermal conductivity, high strength and good wear resistance. It has been widely used in thermal equipment such as power generation boilers, non-ferrous metallurgical furnaces and incinerators.
Low-cement SiC refractory castables use silicon carbide with SiC greater than 97% as refractory aggregate and powder. Add SiO2 ultrafine powder and metallic silicon antioxidant, use CA-70 cement as the binding agent and add polyphosphate water-reducing agent. The main properties of this material are 85% SiC and drying volume density at 110°C. The compressive and flexural strengths are 2.5g/cm3, 45MPa and 9MPa respectively. The wire change, pressure resistance and flexural strength after burning at 1000℃ are -0.2%, 107MPa and 24MPa respectively. The wire change, pressure resistance and flexural strength after burning at 1450℃ are +0.3%, 130MPa and 54MPa respectively. The thermal conductivity at 400℃ is 12.2W/(m·K).
To purchase high-quality low-cement refractory castables, please contact Rongsheng Refractory Materials Manufacturer. Get free refractory lining solutions, samples and quotes. High-quality product that stands up to trial. A strong manufacturer can effectively guarantee the service life of the company’s high-temperature industrial furnace lining. Choose Rongsheng Refractory Manufacturer to extend the service life of furnace linings and save production costs.