Aluminum silicate refractory materials with aluminum oxide (Al2O3) content higher than 48%, and products formed from bauxite or other raw materials with high alumina content through molding and calcining are collectively referred to as high alumina bricks. According to its Al2O3 content, high-alumina bricks can be divided into super high-alumina bricks, first-grade high-alumina bricks, second-grade high-alumina bricks, and third-grade high-alumina bricks.
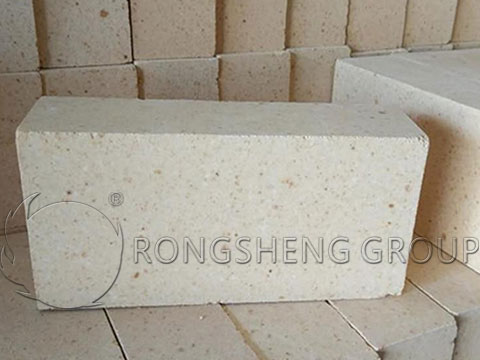
Characteristics of High Alumina Bricks
The product has a small high-temperature creep, strong corrosion-resistance, and good thermal shock stability. High alumina bricks have high thermal stability and good slag resistance. It has opened up the next road to success for the localization of high-quality and high-grade imported refractories required by my country’s new hot blast stoves and has been included in the national “Spark Plan” project.
During use, high alumina bricks will be subjected to physical, chemical, and mechanical effects at high temperatures. They can easily melt or wear due to wear, which can cause cracks and damage, which can interrupt operations and contaminate materials. According to the composition and performance indicators of high alumina bricks, it can be predicted that high alumina bricks will be used at high temperatures.
- For high alumina bricks with special requirements, thermal conductivity, electrical conductivity, and air permeability should also be considered.
- It can resist high temperature and thermal load without softening and melting. High-alumina bricks require high refractoriness.
- It can resist the chemical erosion of molten liquid, dust, and gas without deterioration and corrosion. High alumina bricks are required to have good slag resistance.
- It can resist the effects of rapid temperature changes or uneven heating without cracking or peeling. High alumina bricks are required to have good thermal shock resistance.
- It can resist the erosion, impact, and abrasion of flame, electric charge, and dust, and the surface has no damage. High alumina bricks are required to have high compactness and wear resistance at room temperature and high temperature.
- It can withstand high temperature and thermal load, does not shrink in volume, only expands evenly. High alumina bricks are required to have high volume stability, small residual shrinkage and residual expansion, no crystal shape transformation, and serious volume effects.
- It resists the influence of high-temperature vacuum operation and atmospheric changes, and will not volatilize or damage. High alumina bricks are required to have low vapor pressure and high chemical stability. The appearance is neat and tidy, the specifications and dimensions of the high alumina bricks are accurate, the quality is high, the price is low, and the transportation, construction, and maintenance are convenient.
- It can resist the combined action of high-temperature thermal load and heavy load without losing strength, creep, and collapse. High alumina bricks require higher room temperature strength and high-temperature thermal strength, higher load softening temperature and higher creep resistance.
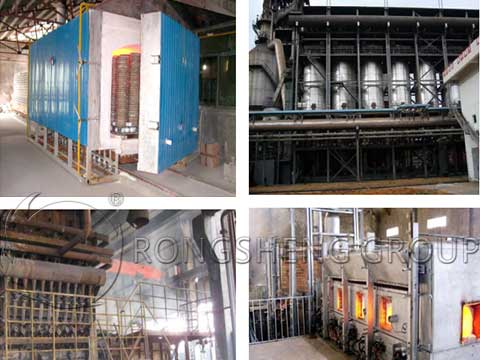
Uses of High Alumina Bricks
The high-aluminum refractory material has high refractoriness and high high-temperature mechanical strength, so it is often used to replace high-quality clay bricks and silica bricks to increase the life of the furnace. At present, it is mainly used to build blast furnaces, hot blast stoves, electric furnace roofs, blast furnaces, reverberatory furnaces, rotary kiln linings, and ventilating partition walls for regenerators of glass furnaces. In addition, high-alumina bricks are also widely used as checker bricks for open-hearth regenerators, plugs, and nozzle bricks for pouring systems.
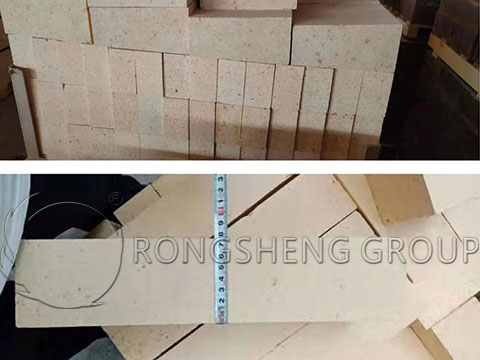
FAQ: What are the differences between low-porosity high-alumina bricks and high-alumina bricks?
The biggest difference between low-porosity high-alumina bricks and high-alumina bricks is the low porosity. Generally, high alumina bricks are divided into one, two, and three grades, and various grades of high alumina bricks are produced according to different indicators. The zirconium component is an anti-stripping high-alumina brick, and the low-porosity high-alumina brick is a special high-alumina brick with low porosity and good thermal shock.
Generally, the pores of high alumina bricks are about 22-24%, and the pores of low-porosity high alumina bricks are less than 18%-19%. The reason for the slight difference in pores between the two is mainly due to the small difference between machines with different pressures during high-pressure molding, but the thermal shock is the same.
Low-porosity high-alumina bricks and general high-alumina bricks are also different in firing time and humidity. Generally, the firing time of high alumina bricks is 60-70 minutes, while the firing time of low porosity high alumina bricks is more than 80 minutes. In this way, the load softening temperature of the two high alumina bricks is also different.
Because low-porosity high-alumina bricks need to be added with specific matrix materials, the firing temperature is also higher than that of general high-alumina bricks, so the compressive strength is also different.
Generally, some high alumina bricks have low-temperature requirements, and some waste high alumina bricks are added in a small proportion, so there is a big difference in production costs.
Low-porosity high-alumina bricks are used in the lining of special kilns, and the corrosion of the atmosphere in the kiln also requires high-alumina bricks. Therefore, low-porosity high-alumina bricks are not only low-porosity, wear-resistant, fatigue-resistant, but also have good corrosion resistance. But the price will be relatively high compared with the general high alumina bricks.
In short, there is a difference in the inherent quality of general high alumina bricks and low porosity high alumina bricks. It can be used according to different situations.