In order to reduce the pollution of hexavalent chrome in magnesia-chrome bricks, the first step is to develop magnesia-chrome bricks with low chrome content. Low chrome magnesia chrome bricks are made of high iron magnesia and chromite. Its technological feature is to use a part of magnesia-iron spinel instead of magnesia-chrome spinel. At high temperatures, Fe2O3 in high-iron magnesia dissolves in periclase crystals. During the cooling process, MgO·Fe2O3 precipitated from the periclase crystals, forming small pitted mafic-iron spinels scattered in the periclase.
The size of the mafic spinel is 1~3μm, and it is tightly wrapped by periclase crystals. Therefore, iron oxide has little effect on the high-temperature performance of refractory materials. In other words, the key point of the process of low chrome magnesia chrome brick is to replace part of the magnesia spinel with magnesia iron spinel. By limiting the harmful effects of Fe2O3 and exerting the beneficial effects of Fe2O3 and Cr2O3 added, the performance and life of the material are maintained.
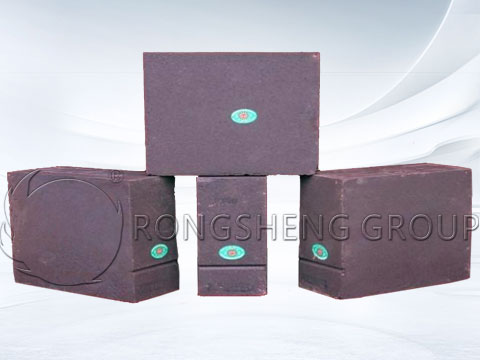
Comparison of Low Chrome Magnesia Chrome Bricks and Direct-Bonded Magnesia Chrome Bricks
Comparison of Low Chrome Magnesia Chrome Bricks and Direct-Bonded Magnesia Chrome Bricks | ||
Properties | Low Chrome Magnesia Chrome Bricks | Direct Bonded Magnesia Chrome Bricks |
Bulk Density g/cm3 | 2.9 | 3.12 |
Hot Flexural Strength (1400℃) MPa | ≈1 | ≈6 |
Creep Rate (1400℃, 24h) % | -0.03 | +0.006 ~ -0.01 |
Reheating Linear Change (1500℃, 6h) % | -0.2 | 0.2 ~ 0.8 |
Load Softening Temperature ℃ | 1650 ~ 1700 | 1650 ~ 1700 |
From the “Comparison table of low chrome magnesia chrome bricks and direct-bonded magnesia chrome bricks”, it can be seen that the physical properties of low chrome magnesia chrome bricks are slightly lower than that of directly bonded magnesia chrome bricks. This is due to the low firing temperature of low chrome magnesia chrome bricks. However, the service life of low chrome magnesia chrome bricks is generally equivalent to that of directly bonded magnesia chrome bricks, and sometimes higher than that of directly bonded magnesia chrome bricks.
Imported refractory materials are formed by hydraulic presses, and the batching, forming, firing, and inspection processes are fully automatically controlled. The products have high dimensional accuracy, uniform quality, and no hidden cracks. Refractory brick manufacturers mainly use friction-pressed bricks. The level of automation in the batching, molding, firing and inspection is low, the product quality fluctuates greatly, and the size deviation is large. In use, in order to prevent the domestic alkaline materials from falling off the bricks, excessive use of steel plates must be used for locking. After the temperature rises, after the refractory material expands greatly, it is easy to be damaged by excessive extrusion.
In addition, some domestic refractory materials have hidden cracks, which are easy to damage in advance during use, thus significantly shortening the service life of refractory materials. Low chrome magnesia chrome bricks have a lower firing temperature. Therefore, its degree of densification is also low and therefore has a lower modulus of elasticity. In this way, after the brick is squeezed, the mechanical stress generated is lower and the damage is less, thereby prolonging the life of the refractory material. In recent years, some domestic refractory factories have reduced the mechanical strength of directly bonded magnesia-chrome bricks, and as a result, the service life has been increased.
However, low chrome magnesia chrome bricks should not be used on the lining of kilns with a high alkali content and an alkali-sulfur ratio greater than 1. Because the free alkali vapor will enter the brick body, corrode the chromite, and form volatile K2CrO4. The chrome content of low chrome bricks is very low. Both the formation of Cr61 and the volatilization of K2CrO4 may destroy the direct bond, causing rapid damage to the refractory. For example, after adopting fly ash ingredients in a new dry process cement kiln in Northeast China, the alkali content of fly ash was not tested. As a result, the R2O content in the clinker increased to more than 1.2%, and the lifespan of low-chrome bricks dropped sharply from 10 to 12 months to 3 to 4 months. The results of electron microscopy showed that K2(Cr, S)O6 was formed in the remaining bricks, and the direct bond was almost destroyed.
Magnesia Chrome Bricks Manufacturer
There are many manufacturers of magnesia chrome bricks, and the strength of the manufacturers is also different. To purchase high-quality magnesia-chrome bricks, please choose a refractory brick manufacturer and sales manufacturer with quality assurance and comprehensive services. Rongsheng refractory material manufacturer has rich experience in refractory material production and sales. Successfully completed a number of turnkey refractory lining material projects, and the customer’s return rate is very high. In the industry, Rongsheng refractory manufacturers have a good reputation. If you have a project that requires refractory lining materials, please contact us. Maybe we can help you solve your existing refractory lining problem. Look forward to cooperating with you.