The main damage mechanism of the MgO-C lining of the refining ladle slag line is the oxidation of C. In addition to the direct oxidation of C, the other major factors are the operating temperature greater than 1650 °C and the high-temperature decompression operation. This is especially true under high temperature and reduced pressure conditions. The refining ladle mainly uses MgO-Cr2O3 bricks and high-alumina bricks as the lining refractories for the slag line and the corrosion resistance area, respectively. Due to the requirements of environmental protection, now all except the AOD ladle have achieved chrome-free. Instead, MgO-C bricks or MgO-CaO-C bricks are used as refractories for the lining of the slag line. Low-carbon MgO-C bricks are used for the lining of the ladle slag line in the vacuum refining of molten steel (including refining of low-carbon and ultra-carbon bricks). MgO-C bricks are used for refining the ladle slag line. The selection of MgO-C bricks or MgO-CaO-C bricks for the refining steel slag line mainly depends on the type of refined steel, slag characteristics, and operating conditions.
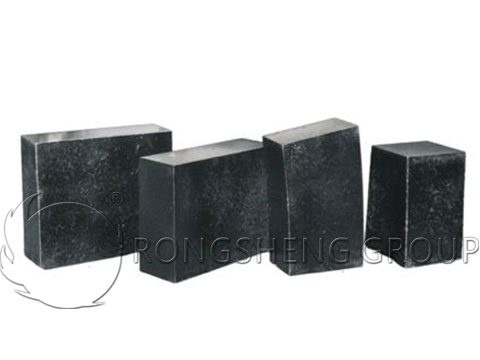
MgO-C Brick for Refining Ladle Slag Line
The aggregate of magnesia-carbon bricks with ladle slag line is generally fused 97.5 (MgO mass fraction ≥ 97.5%), 98 (MgO mass fraction ≥ 98%) ordinary fused magnesia. In the refining with harsh conditions, large crystal fused magnesia is often used. The carbon mass fraction is generally 10% and 12%, and the antioxidants are generally metal aluminum powder, B4C, etc. Compared with magnesia-carbon bricks for converters, the magnesia grade and crystal size of magnesia-carbon bricks for refining ladle slag lines are relatively better.
Among the refining methods currently used, LF refining is the one with the shortest service life, the harshest conditions, and the most serious damage. Generally speaking, the service life of LF refining ladle slag line magnesia-carbon bricks is 1535 times, and the specific conditions vary depending on the specific operation.
In order to strengthen the corrosion resistance of molten slag, the performance of magnesia is very important. Slag line magnesia-carbon bricks generally use more than 97% fused magnesia because the periclase crystals of the magnesia are generally relatively large. In addition, it is generally required that the CaO/SiO2 molar ratio should be greater than 2 as much as possible. In this way, the phases at the periclase grain boundaries are 2CaO·SiO2, 3CaO·SiO2, etc., and the formation of low melting point components such as CaMg(SiO4) and (Mn, Ca)(SiO3) can be avoided as much as possible. It can also effectively inhibit the erosion of slag along the periclase grain boundary.
The resistance of magnesia-carbon bricks to the erosion of slag is not only related to the properties of magnesia but also closely related to the structure of magnesia-carbon bricks. A dense and well-stressed structure will have relatively good corrosion resistance. In addition to the tightest packing of particles, the most important thing is the characteristics, content, and distribution of graphite. The carbon content is beneficial to the slag resistance of magnesia-carbon bricks, but it is used in the smelting of pipeline steel X60~80 used in the petroleum industry and cord steel used in automobile tires. The carbon content of magnesia-carbon bricks is required to be as low as possible, which is the low carbonization of magnesia-carbon bricks.
Get the most competitive product quotes for free, and free sample trials. Please leave your specific needs on the website page, or send us an email directly. We will get back to you as soon as possible.