What is Zirconium Corundum Brick? Zirconia-corundum refractory brick refers to a refractory product with a ZrO2 content of 33%~45% made of industrial alumina powder and selected zircon sand as raw materials.
Zirconium corundum bricks are mainly used in glass industry tank kilns. Zirconium corundum bricks, also known as electric fused bricks, are abbreviated as AZS, which are three chemical components according to the phase diagram of the Al2O3-ZrO2-SiO2 ternary system. Arranged in the order of their content, Al2O3 takes A, ZrO2 takes Z, SiO2 takes S, and the national standard adopts this abbreviation. For example, No. 33 fused-cast zirconium corundum brick, abbreviated as AZS-33#. No. 36 fused-cast zirconium corundum brick, abbreviated as AZS-36#. No. 41 fused-cast zirconium corundum brick, abbreviated as AZS-41#.
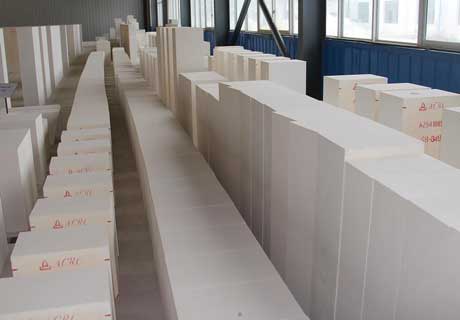
Fused zirconia corundum brick is a refractory material with high quality and excellent high-temperature performance
Fused zirconia corundum brick is a high-quality refractory material with excellent high-temperature performance. It is mainly made of materials such as zirconia and alumina by arc melting. This kind of adobe has the characteristics of high density, high hardness, high heat resistance, and corrosion resistance. It has a good effect in high temperature and chemically aggressive environments.
The adobe is usually used in high-temperature refractory equipment such as high-temperature industrial furnaces, metallurgical furnaces, and glass kilns, and can withstand long-term operation at high temperatures. At the same time, this material is also widely used in the manufacture of components in high-temperature environments such as high-speed trains and aircraft engines.
In the production process, it is first necessary to select high-quality zirconia and alumina raw materials and mix them evenly. Then, the mixture is poured into an electric furnace for high-temperature electric fusion to form a solid adobe. Finally, the adobe is baked and processed to make bricks and components of various specifications and shapes.
It is worth noting that fused zirconia corundum bricks have the characteristics of high preparation process requirements and high production costs. Therefore the price is more expensive. However, its excellent high-temperature performance and corrosion resistance make it widely used in some important industrial and technological fields.
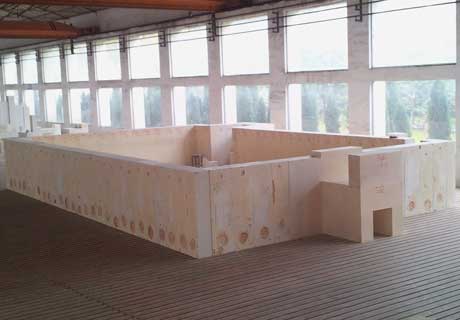
Grades and technical requirements of zirconium corundum bricks for glass kiln
Al2O3-ZrO2-SiO2 series are mainly zirconium corundum bricks and zirconium mullite bricks. In the melting part and working part of the glass tank furnace, when in contact with the molten glass, refractory materials are required to resist erosion, and zirconium corundum has this characteristic and is the preferred material. Zirconia corundum bricks are divided into three grades according to their zirconia content, namely AZS-33#, AZS-36#, and AZS-41#.
Zirconia corundum brick is a white solid formed by pouring pure alumina powder and zircon sand containing 65% zirconia and 34% silicon dioxide into the model after being melted in an electric furnace and cooled. Its petrographic structure is composed of eutectoid and glass phases of corundum and zirconite. Physiologically speaking, it is a eutectoid of the corundum phase and zirconite phase, and the glass phase is filled between their crystals.
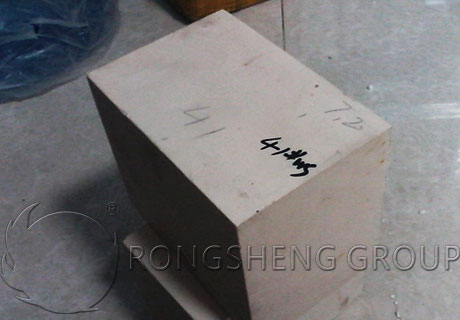
Why is the corrosion resistance of zirconium corundum bricks manufactured under a reducing atmosphere poor?
The contact between the glass phase of the fused zirconia corundum brick and the high-temperature glass liquid will form a high-viscosity layer, which is the key to the good corrosion performance of the zirconia corundum brick. This requires a high softening temperature of the glass phase, so there are fewer other components in the brick except Al2O3, ZrO2, SiO2, and Na2O. However, due to the use of graphite lining bricks and graphite electrodes during electric furnace melting, a reducing atmosphere will be generated. C and CO will reduce part of Fe2O3, TiO2, and SiO2 in the melt to low-valent oxides, which will increase the composition. According to the basic principle of phase ratio, this will lower the liquid phase limit temperature.
When such bricks are used at high temperatures, the viscosity of the glass phase is greatly reduced, and a high-viscosity protective layer cannot be formed. The low viscosity of the glass phase easily diffuses into the high-temperature glass liquid. Therefore, the crystal phase in the brick loses the binder and also falls into the molten glass, which causes streaks and stones in the molten glass. The fused zirconia corundum bricks produced by the oxidation method do not use graphite lining bricks. Although the electrode is still made of graphite, it is melted by a long arc method, so that C is combined with oxygen in the air in the arc to generate CO2 without entering the melt.
The carbon content of bricks produced by this method is less than 0.005%, so the corrosion resistance is greatly increased.
At the same time, zirconium corundum bricks made by the reduction method will also generate bubbles in the glass. This is because the low-valent oxides and other substances such as C in the glass phase of the brick have strong reducing properties, and they will take away the oxygen dissolved in the glass liquid when they contact with the glass liquid. This changes the composition of the gas soluble in the glass into a gas that is not easily soluble in the glass liquid and becomes bubbles. For example, SO3 dissolved in glass liquid is reduced to SO2. The solubility of SO2 in glass liquid is low, so it becomes bubbles. This degrades the quality of the molten glass.
To solve the problem of refractory brick lining for glass kiln, please contact the Rongsheng refractory material manufacturer. Our zirconia corundum bricks are of reliable quality and our refractory service is guaranteed. High-Quality AZS Bricks for Glass Kiln, Glass Kiln Refractory Lining Solutions, Competitive AZS Brick Prices.